What is the quality of PCB assembly?
Another important aspect of PCB assembly is its ability to ensure precise and accurate connections between electronic components. This is achieved through the use of advanced technologies such as surface mount technology (SMT) and through-hole technology (THT), which ensure efficient and reliable connections, improving the overall performance of the product.
Moreover, PCB assembly offers a more efficient and cost-effective solution for electronic manufacturing compared to traditional methods. This is because it allows for a quicker production process with lower labor costs, resulting in faster turnaround times and reduced overall expenses.
In addition to its practical advantages, PCB assembly also offers a variety of design options. With the use of specialized software and machinery, manufacturers can create custom PCB layouts to meet the specific needs and requirements of different products. This allows for greater flexibility in the design process and the ability to optimize the overall performance and functionality of the product.
Furthermore, PCB assembly also plays a crucial role in ensuring the durability and reliability of electronic devices. The use of high-quality materials and stringent quality control processes during assembly results in a longer lifespan for the product, making it a preferred choice for various industries.
With the continuous advancements in technology, PCB assembly continues to evolve and adapt to meet the growing demands of the market. It has become an essential component in the production of modern electronic devices, providing a strong foundation for their functionality, efficiency, and overall success.
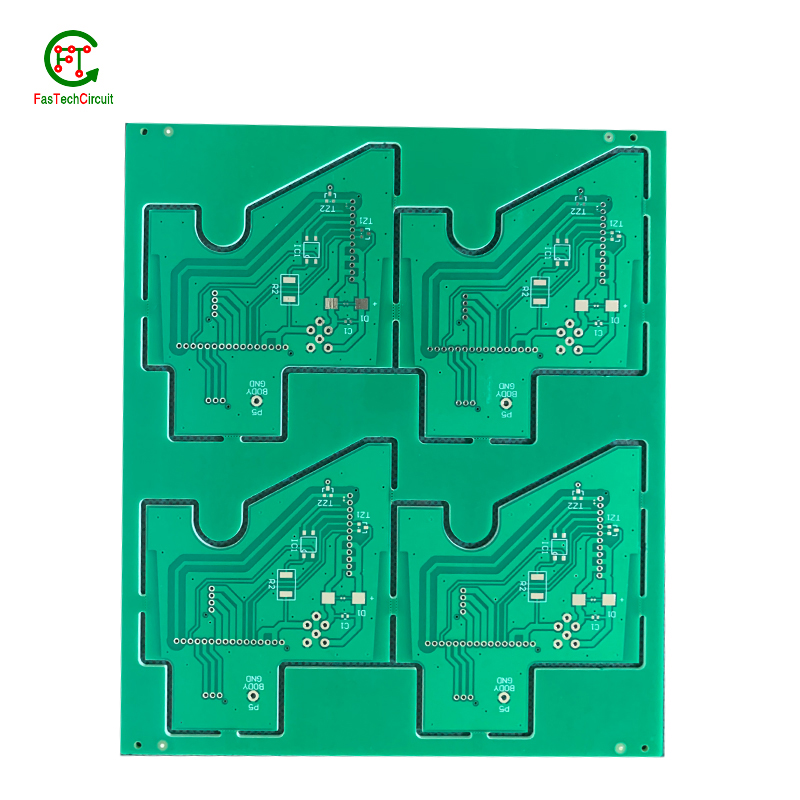
The assembly process begins with the design and layout of the PCB, which dictates the placement and orientation of components. Once the design is finalized, the components are placed using automated equipment or by hand. The PCB is then heated to melt the solder and create permanent connections between the components and the board.
PCB assembly is a critical part of the electronic manufacturing process. The assembly of a PCB involves the use of a variety of components, including passive and active components, which are carefully placed and soldered to create an electronic circuit. Additional processes such as cleaning, coating, and testing are also carried out to ensure the quality and durability of the PCB.
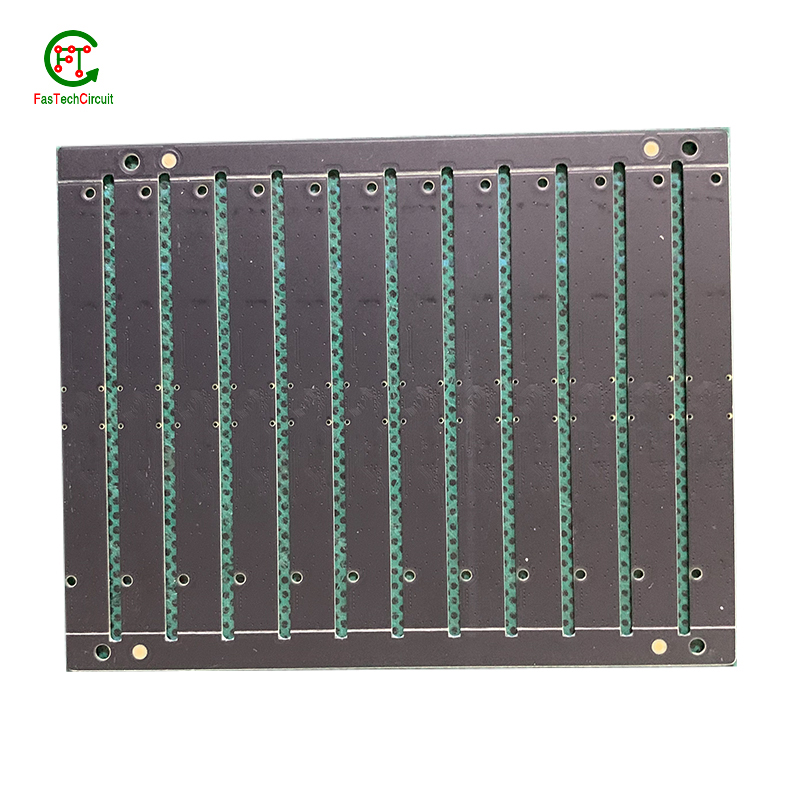
PCB assembly is the process of assembling electronic components onto printed circuit boards (PCBs). It plays a critical role in the production of various electronic devices, from household appliances to advanced industrial equipment. However, as technology advances and the demand for higher quality products increases, there are often concerns and questions regarding the PCB assembly process. In this FQA (Frequently Asked Questions) section, we will address some commonly asked questions to provide a better understanding of PCB assembly.
2.What is main PCB failure?
3.What is the difference between PCB fabrication and PCB assembly?
4.How do you assemble a PCB?
5.How do you calculate PCB assembly cost?
6.What technology is used in PCB?
7.How long does PCB assembly take?
8.Why are PCBs laminated?
1.What is the raw material of PCB assembly?
The raw material of PCB assembly includes: 1. Copper-clad laminate (CCL): This is the base material of the PCB, which is made of layers of fiberglass cloth and epoxy resin with a thin layer of copper on one or both sides. 2. Copper foil: This is the thin layer of copper that is laminated onto the CCL to create the conductive traces and pads on the PCB. 3. Solder mask: This is a layer of polymer resin that is applied over the copper traces to protect them from oxidation and to prevent solder from flowing onto unwanted areas during the assembly process. 4. Silk screen: This is a layer of ink that is applied over the solder mask to add labels, symbols, and other markings to the PCB. 5. Solder paste: This is a mixture of solder alloy particles and flux that is used to attach electronic components to the PCB. 6. Electronic components: These include resistors, capacitors, diodes, transistors, integrated circuits, and other electronic devices that are mounted onto the PCB. 7. Adhesives: These are used to bond components to the PCB and to hold the layers of the PCB together. 8. Flux: This is a chemical substance that is used to clean and prepare the surfaces of the PCB and components for soldering. 9. Solder: This is a metal alloy that is melted and used to create electrical connections between components and the PCB. 10. Lead-free materials: In some cases, lead-free materials may be used in the PCB assembly process to comply with environmental regulations. These materials include lead-free solder, lead-free components, and lead-free flux.
2.What is main PCB failure?
Main PCB failure refers to a malfunction or breakdown of the main printed circuit board (PCB) in an electronic device. The main PCB is responsible for controlling and coordinating the functions of various components in the device, and a failure can result in the device not functioning properly or not functioning at all. This can be caused by various factors such as physical damage, electrical surges, or manufacturing defects. Main PCB failure can be a serious issue and may require professional repair or replacement of the PCB.
3.What is the difference between PCB fabrication and PCB assembly?
PCB fabrication and PCB assembly are two distinct processes involved in the production of a printed circuit board (PCB). PCB fabrication, also known as PCB manufacturing, is the process of creating the bare PCB board by etching copper traces onto a non-conductive substrate. This involves several steps such as designing the PCB layout, printing the circuit onto the substrate, etching the copper traces, and drilling holes for components. The end result of this process is a bare PCB board with copper traces and holes for components. On the other hand, PCB assembly is the process of attaching electronic components onto the bare PCB board to create a functional electronic circuit. This involves placing the components onto the board, soldering them onto the copper traces, and testing the circuit for functionality. The end result of this process is a fully functional PCB that can be used in electronic devices. In summary, PCB fabrication is the process of creating the bare PCB board, while PCB assembly is the process of adding electronic components to the board to create a functional circuit. Both processes are essential in the production of a PCB and are often carried out by different companies or departments within a company.
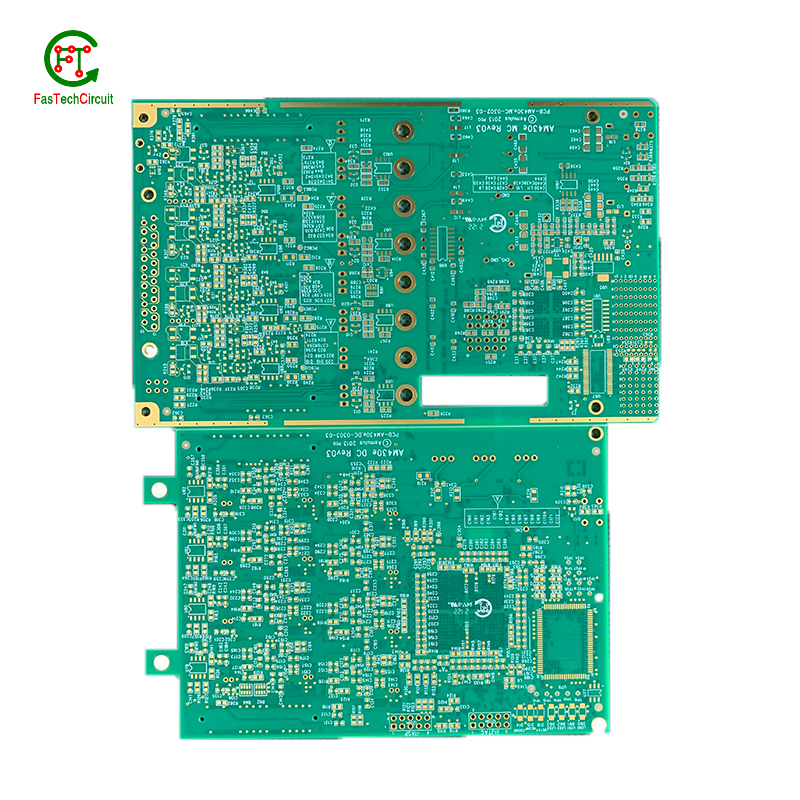
4.How do you assemble a PCB?
1. Gather all necessary materials and tools: - PCB board - Electronic components - Soldering iron - Solder - Flux - Wire cutters - Tweezers - Multimeter - Schematic diagram or layout design 2. Prepare the PCB board: - Clean the board with isopropyl alcohol to remove any dirt or residue - Place the board on a flat and stable surface - Identify the components placement and orientation according to the schematic diagram or layout design 3. Solder the components: - Start with the smallest and lowest height components first - Apply a small amount of flux to the pads on the board - Place the component on the correct pad and hold it in place with tweezers - Heat the pad and component lead with the soldering iron - Once the solder melts, remove the iron and hold the component in place until the solder cools and solidifies - Repeat this process for all components, working from smallest to largest 4. Check for solder bridges: - Use a multimeter to check for any solder bridges between adjacent pads - If any bridges are found, use desoldering braid or a solder sucker to remove the excess solder 5. Test the connections: - Use a multimeter to check for continuity between the component leads and the corresponding pads on the board - Make sure there are no open circuits or short circuits 6. Power up the PCB: - Connect the PCB to a power source and turn it on - Use a multimeter to check for proper voltage levels at different points on the board - Check for any overheating components 7. Troubleshoot and make any necessary adjustments: - If there are any issues with the PCB, use the schematic diagram or layout design to troubleshoot and make any necessary adjustments - Re-solder any loose or faulty connections 8. Secure the PCB: - Once the PCB is functioning properly, secure it in place using screws or standoffs 9. Test the final product: - Connect the PCB to the intended device or circuit and test its functionality - Make any final adjustments if needed.
5.How do you calculate PCB assembly cost?
The cost of PCB assembly can vary depending on several factors such as the complexity of the design, the number of components, the type of components, and the quantity of boards being assembled. To calculate the cost of PCB assembly, you can follow these steps: 1. Determine the cost of components: The first step is to determine the cost of all the components that will be used in the assembly. This includes the cost of the PCB, the cost of the electronic components, and any other materials that will be needed. 2. Calculate the labor cost: The labor cost will depend on the complexity of the design and the number of components that need to be soldered. You can estimate the labor cost by multiplying the number of hours it will take to assemble the PCB by the hourly rate of the assembly technician. 3. Add the cost of equipment and overhead: The cost of equipment and overhead, such as soldering equipment, inspection tools, and facility costs, should also be factored into the total cost. 4. Consider additional services: If you require additional services such as testing, programming, or conformal coating, you will need to add these costs to the total. 5. Calculate the total cost: Once you have determined all the individual costs, add them together to get the total cost of PCB assembly. It is important to note that the cost of PCB assembly can vary significantly depending on the manufacturer and the location. It is recommended to get quotes from multiple manufacturers to compare prices and choose the most cost-effective option.
6.What technology is used in PCB?
1. Printed Circuit Board (PCB) Design Software: PCB design software is used to create the layout and design of the PCB. Popular software includes Altium Designer, Eagle PCB, and KiCad. 2. Computer-Aided Manufacturing (CAM) Software: CAM software is used to convert the PCB design into machine-readable instructions for the manufacturing process. 3. Computer-Aided Design (CAD) Software: CAD software is used to create 3D models of the PCB and its components, allowing for more accurate design and testing. 4. Computer Numerical Control (CNC) Machines: CNC machines are used to drill, cut, and etch the PCB according to the design specifications. 5. Surface Mount Technology (SMT): SMT is a method of placing and soldering electronic components directly onto the surface of the PCB, allowing for smaller and more compact designs. 6. Through-Hole Technology (THT): THT is a method of inserting electronic components through holes in the PCB and soldering them on the other side. 7. Soldering Equipment: Soldering equipment is used to melt and apply solder to the connections between components and the PCB. 8. Automated Optical Inspection (AOI) Systems: AOI systems use cameras and software to inspect the PCB for defects and ensure quality control during the manufacturing process. 9. X-Ray Inspection Systems: X-ray inspection systems are used to detect hidden defects in the PCB, such as faulty connections or missing components. 10. Automated Test Equipment (ATE): ATE is used to test the functionality of the PCB and its components, ensuring that they meet design specifications and function properly.
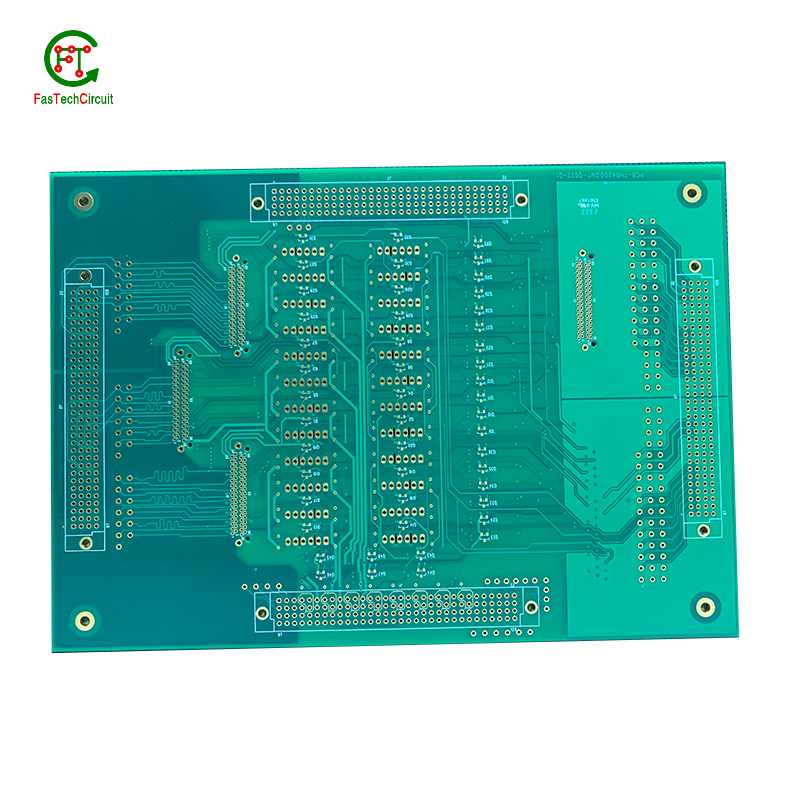
7.How long does PCB assembly take?
The time it takes for PCB assembly can vary depending on the complexity of the design, the number of components, and the manufacturing process used. Generally, it can take anywhere from a few hours to several weeks to complete PCB assembly. Here are some factors that can affect the time it takes for PCB assembly: 1. Design complexity: The more complex the design, the longer it will take to assemble the PCB. This is because complex designs require more time for layout, component placement, and soldering. 2. Number of components: The more components that need to be placed on the PCB, the longer it will take to assemble. Each component needs to be carefully placed and soldered, which can be a time-consuming process. 3. Manufacturing process: The type of manufacturing process used can also affect the time it takes for PCB assembly. For example, hand soldering can take longer than automated assembly processes. 4. Availability of components: If all the components needed for the PCB assembly are readily available, the process can be completed faster. However, if some components are out of stock or need to be ordered, it can add to the overall assembly time. 5. Quality control: Quality control checks are an important part of PCB assembly and can add to the overall time it takes to complete the process. These checks ensure that the PCB is assembled correctly and meets the required specifications. Overall, the time it takes for PCB assembly can range from a few hours for simple designs to several weeks for more complex designs. It is important to work closely with your PCB manufacturer to get an accurate estimate of the assembly time for your specific project.
8.Why are PCBs laminated?
PCBs (printed circuit boards) are laminated for several reasons: 1. Protection: The lamination process adds a layer of protection to the PCB, making it more durable and resistant to damage from external factors such as moisture, dust, and heat. 2. Insulation: The lamination process also adds insulation to the PCB, preventing electrical shorts and ensuring proper functioning of the circuit. 3. Adhesion: Lamination helps to bond the different layers of the PCB together, ensuring that they stay in place and do not shift or separate during use. 4. Stability: Lamination helps to stabilize the PCB, preventing warping or bending that could affect the performance of the circuit. 5. Surface finish: The lamination process can also add a smooth and uniform surface finish to the PCB, making it easier to solder components onto the board. 6. Cost-effective: Lamination is a cost-effective way to manufacture PCBs, as it allows for multiple layers to be bonded together in a single process. 7. Customization: Lamination allows for the customization of PCBs, as different materials and thicknesses can be used to meet specific design requirements.
RELATED NEWS
pcb board manufacturing How To Contact US
PCB from 1 to 30 layers, HDI, Heavy Copper, Rigid-flex board with "pcb board manufacturing One-Stop" service.