What are the major components included in a PCB assembly?
The PCB Assembly process is an essential step in the production of electronic devices such as computers, smartphones, and electronic appliances. It consists of various stages, including component placement, solder paste application, reflow soldering, and final inspection. These stages require precision and attention to detail to ensure the proper functioning of the electronic assembly.
The advantages of PCB Assembly include increased efficiency, reduced manual labor, smaller size, and improved product quality. By automating the process, PCB Assembly can be done at a faster rate, resulting in higher production output. It also eliminates the need for manual wiring and reduces potential human error, resulting in more reliable and higher quality products.
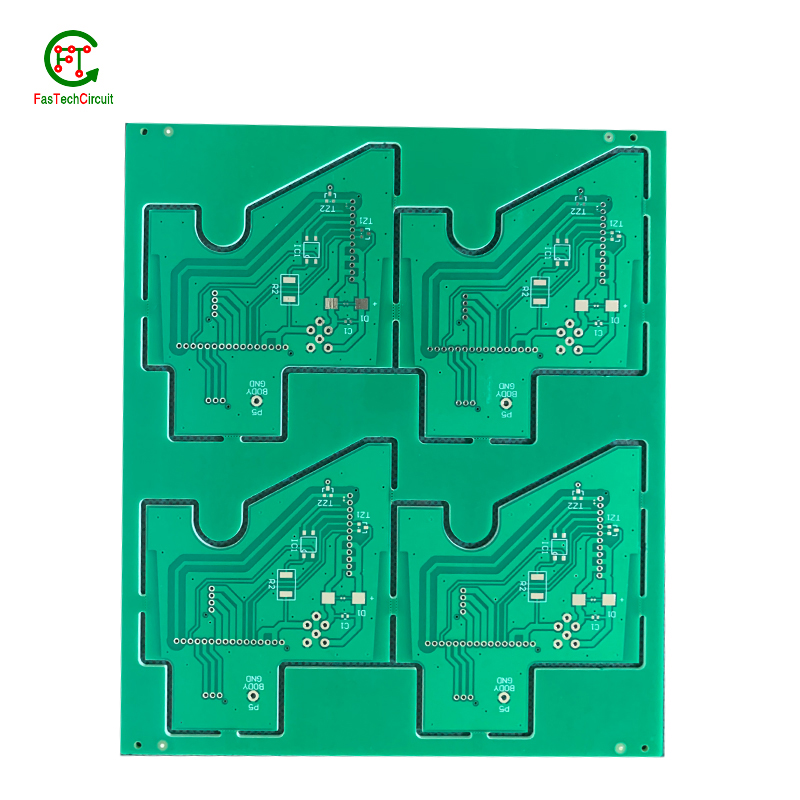
Our advanced PCB assembly services are the perfect solution for achieving precise electronic integration. With state-of-the-art technology and a team of skilled technicians, we ensure the highest quality assembly for your printed circuit boards. From surface mount to through-hole components, we guarantee a flawless assembly that meets your exact specifications and exceeds your expectations.
Our commitment to quality is unmatched, which is why we implement industry-leading quality control measures to ensure zero defect assemblies. From strict material sourcing to thorough inspections and testing, we leave no room for error. We strive for perfection in every stage of the assembly process, resulting in top-quality PCBS that meet the highest standards.
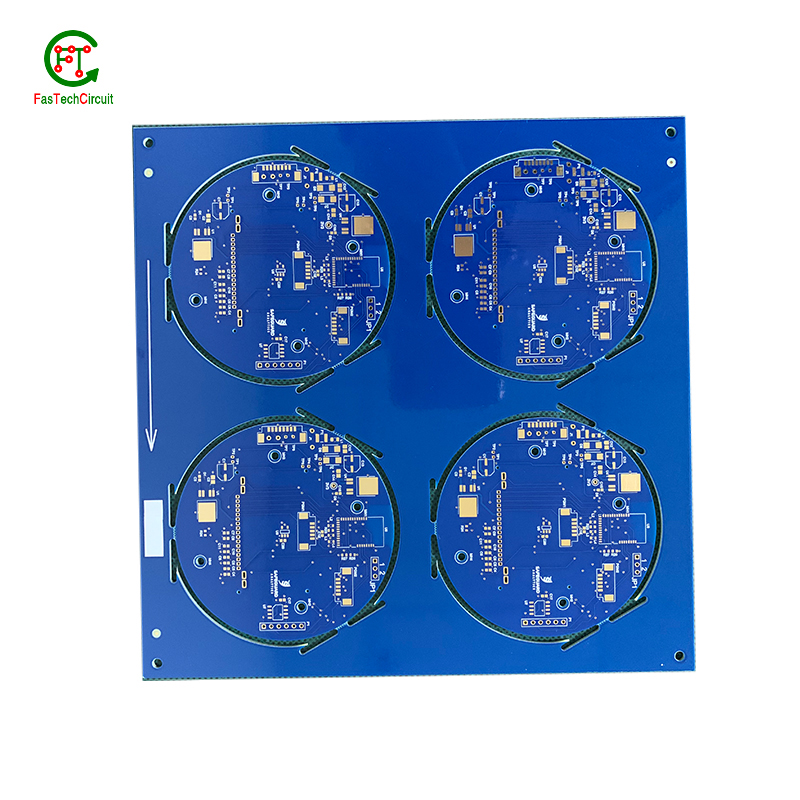
PCB assembly is the process of preparing, placing, and soldering various electronic components onto a printed circuit board (PCB). This involves creating a complete and functional electronic system by interconnecting different components such as capacitors, resistors, integrated circuits, and connectors on a PCB. The assembly process requires precise and accurate placement of components, careful soldering techniques, and thorough quality control measures to ensure proper functioning of the final product. In this introduction, we will discuss the various stages of PCB assembly and the importance of each step in creating a reliable and efficient electronic system.
2.How are PCB assemblies manufactured and assembled?
3.What are the major components included in a PCB assembly?
4.Can PCB assemblies be customized for specific applications?
5.What is the role of surface mount technology in PCB assembly?
6.What are the main challenges faced in PCB assembly process?
7.Can a PCB assembly be repaired if it gets damaged?
8.How important is quality control in the production of PCB assemblies?
9.What factors should be considered when choosing a PCB assembly manufacturer?
10.What is a PCB assembly and how does it differ from traditional circuit assembly?
11.How long does it typically take to complete a PCB assembly project?
12.How has automation and robotics impacted the PCB assembly industry?
13.What steps are taken to ensure compatibility between the PCB assembly and other components?
1.How are environmental regulations and sustainability considerations addressed in PCB assembly?
Environmental regulations and sustainability considerations are addressed in PCB assembly in several ways:
1. Compliance with regulations: PCB assembly companies must comply with various environmental regulations, such as the Restriction of Hazardous Substances (RoHS) directive, which restricts the use of certain hazardous substances in electronic products. They must also adhere to regulations related to waste management, air and water pollution, and worker safety.
2. Use of environmentally friendly materials: PCB assembly companies are increasingly using environmentally friendly materials, such as lead-free solder, to reduce the environmental impact of their products. They also use materials that are recyclable and biodegradable.
3. Energy efficiency: PCB assembly companies are implementing energy-efficient practices in their manufacturing processes, such as using energy-efficient equipment and optimizing production processes to reduce energy consumption.
4. Waste reduction and recycling: PCB assembly companies have implemented waste reduction and recycling programs to minimize the amount of waste generated during the manufacturing process. This includes recycling of materials such as metals, plastics, and electronic components.
5. Sustainable packaging: PCB assembly companies are using sustainable packaging materials, such as biodegradable or recyclable materials, to reduce the environmental impact of their products.
6. Life cycle assessment: PCB assembly companies conduct life cycle assessments to evaluate the environmental impact of their products from raw material extraction to end-of-life disposal. This helps them identify areas for improvement and make more sustainable decisions.
7. Collaboration with suppliers: PCB assembly companies work closely with their suppliers to ensure that the materials and components used in their products are environmentally friendly and comply with regulations.
8. Continuous improvement: PCB assembly companies are continuously seeking ways to improve their environmental performance and sustainability practices. This includes investing in new technologies and processes that are more environmentally friendly and conducting regular audits to identify areas for improvement.
2.How are PCB assemblies manufactured and assembled?
1. Design and Layout: The first step in manufacturing a PCB assembly is to design and layout the circuit board. This involves creating a schematic diagram of the circuit and then using specialized software to design the layout of the components on the board.
2. PCB Fabrication: Once the design is finalized, the PCB is fabricated. This involves printing the circuit pattern onto a copper-clad board using a photosensitive process. The board is then etched to remove the unwanted copper and create the circuit traces.
3. Component Procurement: The next step is to procure all the necessary components for the assembly. This includes electronic components such as resistors, capacitors, integrated circuits, and connectors.
4. Solder Paste Application: Solder paste is a mixture of tiny solder particles and flux. It is applied to the PCB using a stencil, which ensures precise placement of the paste on the board.
5. Pick and Place: Once the solder paste is applied, the components are placed on the board using a pick and place machine. This machine uses a vacuum nozzle to pick up the components and place them on the correct location on the board.
6. Reflow Soldering: After the components are placed, the board is passed through a reflow oven. The oven heats the board to a specific temperature, causing the solder paste to melt and create a strong bond between the components and the board.
7. Inspection: Once the board has been soldered, it goes through a visual inspection to check for any defects or missing components. Automated optical inspection (AOI) machines are often used for this process.
8. Testing: After inspection, the board is tested to ensure that it functions correctly. This can include functional testing, in-circuit testing, and boundary scan testing.
9. Final Assembly: Once the PCB assembly is tested and approved, it is ready for final assembly. This can include adding any additional components, such as connectors or heat sinks, and mounting the board into its final enclosure.
10. Quality Control: The final step is quality control, where the assembled PCB is checked for any defects or issues. This ensures that the final product meets the required specifications and is ready for use.
3.What are the major components included in a PCB assembly?
1. Printed Circuit Board (PCB): This is the base material on which all the components are mounted and connected.
2. Components: These are the electronic parts that are mounted on the PCB, such as resistors, capacitors, diodes, transistors, integrated circuits, etc.
3. Solder: This is the material used to create electrical connections between the components and the PCB.
4. Solder paste: This is a mixture of solder and flux used to attach surface mount components to the PCB.
5. Flux: This is a chemical substance used to clean and prepare the surfaces of the PCB and components for soldering.
6. Solder mask: This is a protective layer applied to the PCB to prevent solder from flowing to unwanted areas.
7. Silkscreen: This is a layer of ink printed on the PCB to label and identify components, test points, and other important information.
8. Copper traces: These are thin lines of copper that connect the components on the PCB and carry electrical signals.
9. Vias: These are small holes drilled through the PCB to allow electrical connections between different layers of the board.
10. Surface finish: This is a coating applied to the exposed copper traces to protect them from oxidation and ensure good solderability.
11. Test points: These are designated areas on the PCB used for testing and troubleshooting during the assembly process.
12. Connectors: These are components used to connect the PCB to other electronic devices or systems.
13. Power sources: These are components such as batteries or power supplies that provide the necessary power for the PCB to function.
14. Heat sinks: These are components used to dissipate heat generated by high-power components on the PCB.
15. Enclosure: This is the outer casing that houses the PCB and protects it from external elements.
16. Labels and documentation: These are important for identifying the PCB and providing information about its components, specifications, and usage.
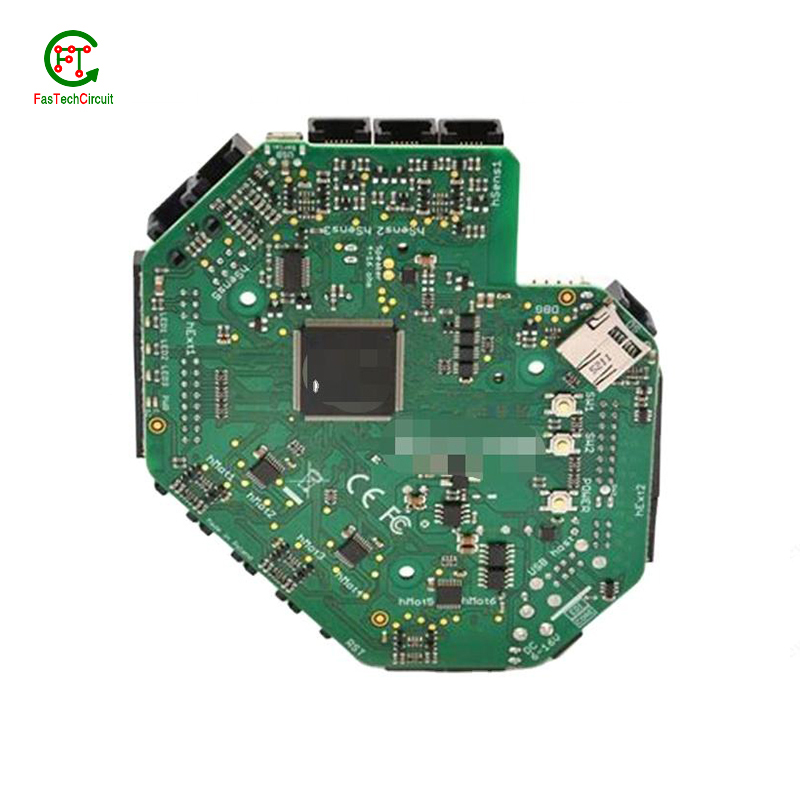
4.Can PCB assemblies be customized for specific applications?
Yes, PCB assemblies can be customized for specific applications. This can include designing the PCB layout and components to meet the specific requirements of the application, such as size, power consumption, and functionality. Additionally, specialized components or features can be added to the PCB assembly to meet the unique needs of the application. This customization process may involve working closely with the PCB manufacturer and/or a design engineer to ensure the final product meets the desired specifications.
5.What is the role of surface mount technology in PCB assembly?
Surface mount technology (SMT) is a method of electronic component placement on a printed circuit board (PCB) that involves directly mounting components onto the surface of the board. This is in contrast to through-hole technology, where components are inserted into holes drilled into the board.
The role of SMT in PCB assembly is to provide a more efficient and cost-effective method of assembling electronic circuits. Some of the key benefits of SMT include:
1. Higher component density: SMT allows for smaller and more compact designs, as components can be placed closer together on the surface of the board.
2. Faster assembly: SMT components can be placed and soldered onto the board using automated machines, which speeds up the assembly process and reduces the need for manual labor.
3. Cost-effective: SMT reduces the amount of material and labor required for PCB assembly, making it a more cost-effective option for high-volume production.
4. Improved performance: SMT components have shorter lead lengths, which reduces the parasitic effects and improves the overall performance of the circuit.
5. Compatibility with modern components: Many modern electronic components are only available in surface mount packages, making SMT essential for incorporating these components into PCB designs.
Overall, the role of SMT in PCB assembly is to provide a more efficient, cost-effective, and reliable method of assembling electronic circuits. It has become the standard method of PCB assembly in the electronics industry and continues to evolve with advancements in technology.
6.What are the main challenges faced in PCB assembly process?
1. Component Placement: One of the main challenges in PCB assembly is accurately placing the components on the board. This requires precision and can be time-consuming, especially for complex designs with a large number of components.
2. Soldering: Soldering is a critical step in the PCB assembly process and requires skilled technicians to ensure proper connections and avoid defects such as cold joints or solder bridges.
3. Component Compatibility: Ensuring that all components are compatible with each other and the PCB design is crucial. Any mismatch can lead to malfunctioning or failure of the circuit.
4. Quality Control: Maintaining quality control throughout the assembly process is essential to ensure the final product meets the required standards. This includes checking for defects, proper component placement, and soldering.
5. Miniaturization: With the increasing demand for smaller and more compact electronic devices, PCB assembly is becoming more challenging due to the need for smaller components and tighter spacing between them.
6. Thermal Management: As electronic devices become more powerful, managing heat dissipation becomes a significant challenge in PCB assembly. Improper thermal management can lead to component failure and reduced lifespan of the device.
7. Design Changes: Changes in the PCB design during the assembly process can cause delays and increase costs. It is essential to have a well-defined and finalized design before starting the assembly process.
8. Lead-Free Soldering: The use of lead-free soldering has become a standard in many countries due to environmental concerns. However, lead-free soldering requires higher temperatures and can be more challenging to work with, leading to increased defects.
9. Component Counterfeiting: The rise of counterfeit electronic components in the market poses a significant challenge in PCB assembly. These components can be of poor quality and lead to product failure, making it crucial to source components from reliable suppliers.
10. Cost and Time Constraints: PCB assembly can be a time-consuming and costly process, especially for complex designs. Meeting tight deadlines and keeping costs under control can be a significant challenge for manufacturers.
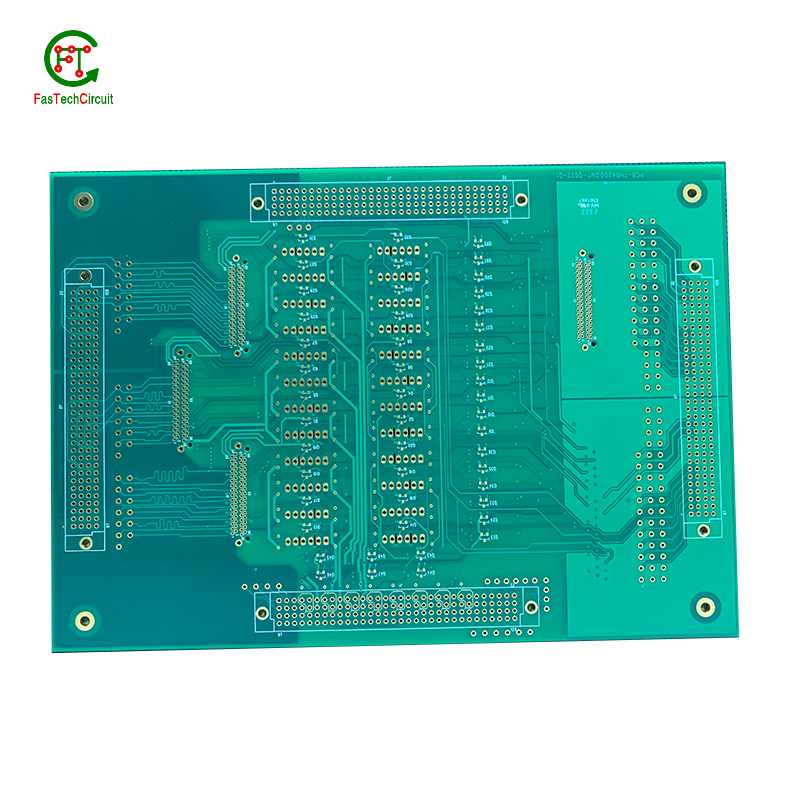
7.Can a PCB assembly be repaired if it gets damaged?
Yes, a PCB assembly can be repaired if it gets damaged. The extent of the damage and the availability of replacement components will determine the feasibility and cost of the repair. In some cases, it may be more cost-effective to replace the entire PCB assembly rather than attempting to repair it. However, if the damage is minor and the necessary components are readily available, a skilled technician can repair the PCB assembly.
8.How important is quality control in the production of PCB assemblies?
Quality control is extremely important in the production of PCB assemblies. PCB assemblies are used in a wide range of electronic devices, from simple household appliances to complex medical equipment. These devices often have critical functions and any defects in the PCB assembly can lead to malfunctions or failures, which can have serious consequences.
Quality control ensures that the PCB assemblies meet the required specifications and standards, and are free from defects. This involves rigorous testing and inspection at various stages of the production process, from the initial design to the final assembly. Quality control also involves identifying and addressing any issues or defects that may arise during production, to ensure that the final product is of the highest quality.
In addition, quality control helps to prevent costly rework or recalls, which can have a significant impact on the production schedule and budget. It also helps to maintain the reputation of the manufacturer and build trust with customers, as they can be confident in the reliability and performance of the PCB assemblies.
Overall, quality control is crucial in the production of PCB assemblies to ensure that they meet the required standards and function properly, which ultimately leads to customer satisfaction and the success of the product.
9.What factors should be considered when choosing a PCB assembly manufacturer?
1. Quality and Reliability: The most important factor to consider is the quality and reliability of the PCB assembly manufacturer. This includes their track record, certifications, and quality control processes.
2. Experience and Expertise: It is important to choose a manufacturer with a proven track record and experience in producing PCB assemblies for your specific industry or application. They should also have a team of skilled engineers and technicians who are knowledgeable about the latest technologies and techniques.
3. Manufacturing Capabilities: The manufacturer's production capabilities should match your project requirements in terms of volume, complexity, and turnaround time. They should have the necessary equipment, facilities, and resources to handle your project efficiently.
4. Cost and Pricing: While cost should not be the only factor, it is important to consider the manufacturer's pricing structure and whether it fits within your budget. It is also important to consider the overall value and quality of their services.
5. Location and Logistics: The location of the manufacturer can impact the cost and speed of delivery. It is important to consider the proximity of the manufacturer to your location and their ability to handle shipping and logistics.
6. Communication and Customer Service: A good PCB assembly manufacturer should have clear and open communication channels and provide excellent customer service. They should be responsive to your inquiries and provide regular updates on the progress of your project.
7. Quality Control Processes: The manufacturer should have robust quality control processes in place to ensure that the final product meets your specifications and industry standards. This includes testing and inspection procedures.
8. Flexibility and Customization: Depending on your project requirements, you may need a manufacturer who can offer customized solutions and adapt to changes in design or specifications. It is important to discuss this with the manufacturer beforehand.
9. Supply Chain Management: The manufacturer should have a reliable supply chain management system in place to ensure timely delivery of components and materials. This is especially important for projects with tight deadlines.
10. Reviews and References: It is always a good idea to research the manufacturer's reputation and read reviews from previous customers. You can also ask for references and speak to other companies who have worked with the manufacturer to get their feedback and recommendations.
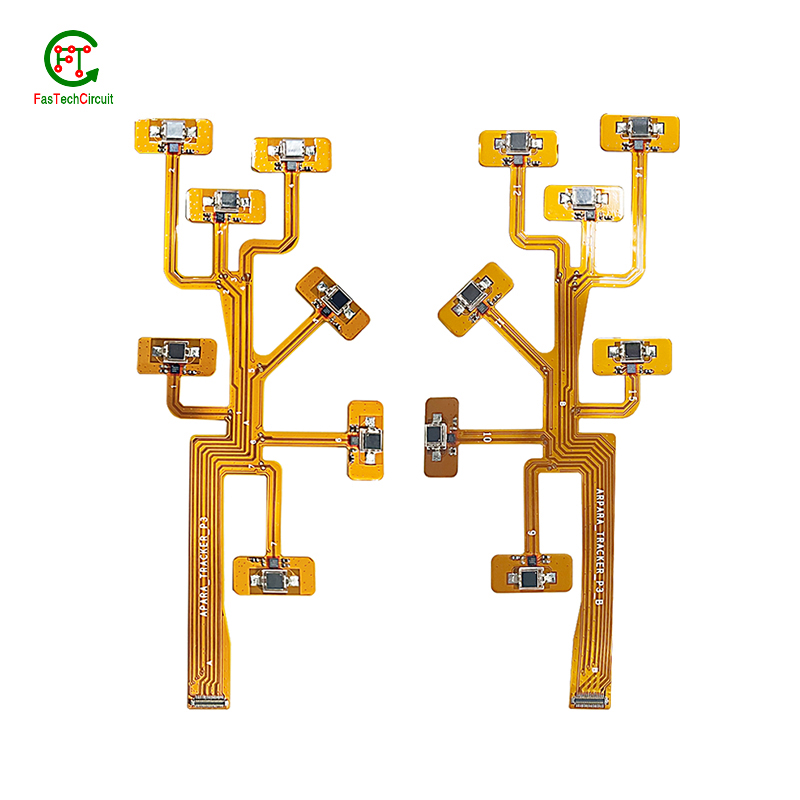
10.What is a PCB assembly and how does it differ from traditional circuit assembly?
A PCB (Printed Circuit Board) assembly is the process of attaching electronic components to a printed circuit board in order to create a functional electronic circuit. This process involves soldering or other methods of attaching the components to the board, as well as testing and inspection to ensure proper functionality.
The main difference between PCB assembly and traditional circuit assembly is the use of a printed circuit board. In traditional circuit assembly, the components are typically connected by wires or other means on a non-conductive surface, such as a breadboard. This method is often used for prototyping and testing purposes, but is not suitable for mass production.
PCB assembly, on the other hand, allows for a more efficient and reliable production process. The components are mounted directly onto the board, which is designed with specific traces and pads to connect the components and create a complete circuit. This method is commonly used in the manufacturing of electronic devices, as it allows for faster production and higher quality control.
Overall, PCB assembly offers a more streamlined and cost-effective approach to circuit assembly, making it the preferred method for mass production of electronic devices.
11.How long does it typically take to complete a PCB assembly project?
The time it takes to complete a PCB assembly project can vary depending on the complexity of the project, the number of components, and the availability of materials. However, on average, a PCB assembly project can take anywhere from 1-4 weeks to complete. This includes the time for ordering materials, PCB fabrication, component placement, soldering, testing, and final inspection. Some projects may take longer if there are any design changes or if there are delays in receiving materials. It is important to communicate with your PCB assembly provider to get a more accurate timeline for your specific project.
12.How has automation and robotics impacted the PCB assembly industry?
1. Increased Efficiency and Productivity: Automation and robotics have greatly increased the speed and accuracy of PCB assembly processes. This has led to a significant increase in efficiency and productivity, as machines can work faster and longer without breaks or errors.
2. Improved Quality Control: With automation and robotics, the chances of human error in PCB assembly are greatly reduced. This results in higher quality products and fewer defects, leading to improved customer satisfaction and reduced costs for rework or repairs.
3. Cost Savings: Automation and robotics have reduced the need for manual labor in PCB assembly, resulting in cost savings for manufacturers. This is especially beneficial for high-volume production, as machines can work continuously without the need for breaks or overtime pay.
4. Flexibility and Customization: Automated PCB assembly machines can be programmed to handle a wide range of components and PCB designs, making it easier to produce customized or complex PCBs. This flexibility allows manufacturers to meet the demands of a diverse customer base.
5. Reduced Lead Times: With automation and robotics, the time required for PCB assembly is significantly reduced. This allows manufacturers to meet tight deadlines and deliver products to customers faster, improving their competitiveness in the market.
6. Safer Working Environment: PCB assembly involves handling hazardous materials and working with high temperatures and precision tools. Automation and robotics have reduced the need for human involvement in these processes, making the working environment safer for employees.
7. Integration with Industry 4.0: Automation and robotics have enabled the integration of PCB assembly processes with Industry 4.0 technologies such as data analytics, artificial intelligence, and the Internet of Things. This allows for real-time monitoring and optimization of production processes, leading to further improvements in efficiency and quality.
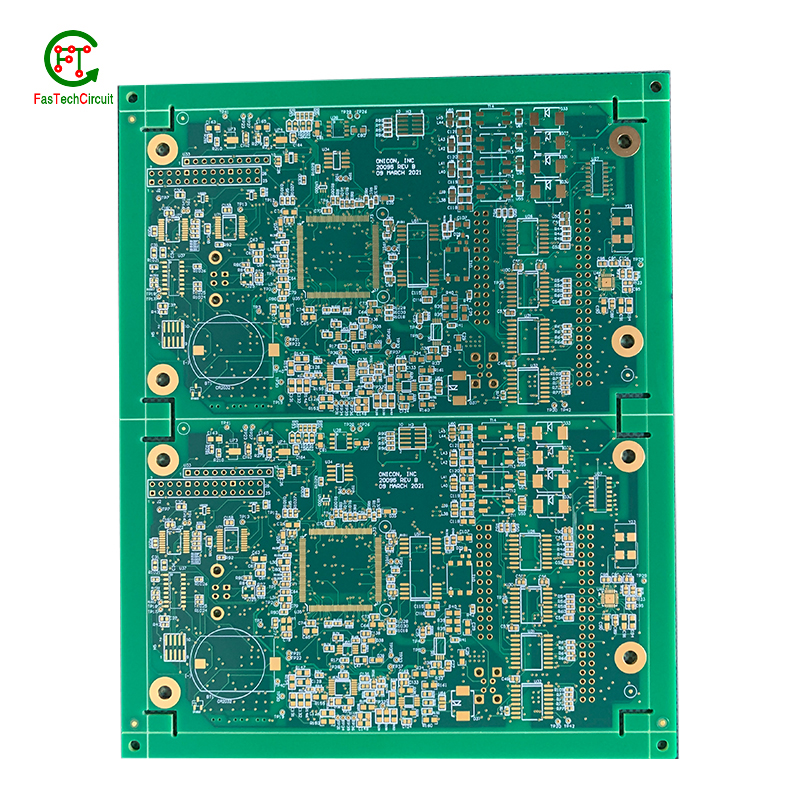
13.What steps are taken to ensure compatibility between the PCB assembly and other components?
1. Design review: The first step is to conduct a thorough design review of the PCB assembly and other components to identify any potential compatibility issues. This involves checking the specifications, dimensions, and electrical requirements of each component.
2. Component selection: During the design phase, components are carefully selected based on their compatibility with the PCB assembly. This includes considering factors such as voltage, current, temperature range, and physical dimensions.
3. Prototyping: Before mass production, a prototype of the PCB assembly is usually created to test its compatibility with other components. This allows any issues to be identified and resolved before production begins.
4. Simulation and testing: Simulation software can be used to simulate the behavior of the PCB assembly and other components in a virtual environment. This helps to identify any potential issues and allows for adjustments to be made before production.
5. Compliance with standards: The PCB assembly and other components must comply with industry standards and regulations to ensure compatibility. This includes standards for electrical, mechanical, and environmental requirements.
6. Communication with suppliers: It is important to communicate with the suppliers of the PCB assembly and other components to ensure that they are aware of the compatibility requirements. This allows for any potential issues to be addressed before production.
7. Quality control: During the production process, quality control measures are implemented to ensure that the PCB assembly and other components are manufactured to the required specifications. This includes testing for compatibility and functionality.
8. Assembly process: The assembly process must be carefully planned and executed to ensure that the PCB assembly and other components are assembled correctly and in a way that ensures compatibility.
9. Post-assembly testing: After the PCB assembly and other components are assembled, they undergo thorough testing to ensure that they are functioning correctly and are compatible with each other.
10. Ongoing monitoring: Even after the PCB assembly and other components are assembled and tested, ongoing monitoring is important to ensure that they continue to function correctly and remain compatible with each other.
RELATED NEWS
pcb board manufacturing How To Contact US
PCB from 1 to 30 layers, HDI, Heavy Copper, Rigid-flex board with "pcb board manufacturing One-Stop" service.