ac plug pcb design
Our managers and technicians are all experienced personnel who have been engaged in the PCB industry for more than 20 years, so we have rich production management experience and professional PCB skills. We constantly introduce new equipment, new technologies, and use high-quality materials to ensure the quality of PCB products. We have professional technical personnel who can provide early design consultation and technical support, making customers more worry-free. With high-quality and reliable products, advanced technology and value-added services, our products are very popular in Azerbaijan,Eritrea,Iceland,Tonga,Tunisia,Turks and Caicos Islands, the United States and Japan. Won high praise from customers.
Base Material | FR-4/CEM-1/CEM-3/Polyimild/PTFE/Rogers |
Board Thickness | 0.2-5mm |
Model Number | Custom PCB & PCB Assembly |
Type | Aluminum PCB |
Brand Name | FC |
Copper Thickness | 0.2-2mil(11-44um) |
Min. Hole Size | 0.1mm(4mil)for HDI / 0.15mm(6mil) |
Min. Line Width | 0.075mm/0.075mm(3mil/3mil) |
Min. Line Spacing | 0.003'' |
Surface Finishing | HASL/OSP/Ag/ENIG/ENEPIG/Immersion silver/Tin |
Board Size | Custom |
Model Number | Customized |
Base Material | FR4 Aluminum CEM-1 94V0 |
Surface Finishing | HASLENIG OSP |
Number of layer | 1-16layer |
Other service | Components purchasing and assem |
ly Solder mask | White Black Green Blue,Red,etc. |
Dsign service | Available |
Testing | Function testing |
Certificate | RoHS, ISO/TS16949, ISO9001 |
Name | High Quality led light aluminum pcb printed circuit board |
Packaging Details | Vaccum package and standard carton outside High Quality led light aluminum pcb printed circuit board |
Supply Ability | 59074 Square Meter/Square Meters per Month |
Quantity (pieces) | > 28589 |
Lead time (days) | 12 |
ac plug pcb design bearings FAQs Guide Welcome to our state-of-the-art PCB (Printed Circuit Board) products. We are proud to offer a comprehensive range of high-quality and versatile PCB solutions to meet the constantly evolving needs of the modern electronics industry.Our PCBs are expertly designed and manufactured using the latest technology and advanced techniques, ensuring reliability, durability, and exceptional performance for a wide range of applications. We understand the importance of precision and attention to detail in the production of PCBs and we are committed to meeting stringent quality standards.
2.What are the most common uses for ac plug pcb design?
3.How are components selected for a ac plug pcb design design?
4.What type of material is used for the silkscreen on a ac plug pcb design?
5.How are signal integrity issues addressed in ac plug pcb design design?
6.What is the difference between a copper pour and a trace on a ac plug pcb design?
7.What techniques are used for reducing electromagnetic interference (EMI) on a ac plug pcb design?
8.What are the main components of a ac plug pcb design?
9.What is the purpose of a ground plane on a ac plug pcb design?
10.What materials are used to make a ac plug pcb design?
11.What is the minimum size of a through-hole component that can be used on a ac plug pcb design?
12.Can a ac plug pcb design be repaired if damaged?
13.What is the maximum size of a ac plug pcb design?
14.What is the role of automated optical inspection (AOI) in ac plug pcb design production?
15.What types of ac plug pcb designs are there?
1.Can ac plug pcb designs be used in high-frequency applications?
Our mission is to provide customers with the best solutions for ac plug pcb design.
Yes, PCBs (printed circuit boards) can be used in high-frequency applications. However, the design and construction of the PCB must be carefully considered to ensure optimal performance at high frequencies. This includes using specialized materials, such as high-frequency laminates, and implementing proper grounding and shielding techniques. Additionally, the layout and routing of the PCB must be optimized to minimize signal loss and interference.
2.What are the most common uses for ac plug pcb design?
We enjoy high authority and influence in the industry and continue to innovate products and service models.
Printed circuit boards, or PCBs, are widely used in electronic devices and equipment. They are used in everything from smartphones and computers to household appliances and automotive systems. PCBs are essential components for connecting electrical and electronic components together, providing a robust and reliable platform for digital and analog signals to pass through. Common uses for PCBs include controlling and powering electronic devices, storing and processing data, and providing a means of communication between components. They are also used in various industrial and commercial applications, such as automation and control systems, medical equipment, and aerospace technology. PCBs offer a cost-effective and efficient solution for creating complex electronic circuits, making them a crucial component in modern technology.
3.How are components selected for a ac plug pcb design design?
We pay attention to employee development and benefits, and provide a good working environment in order to improve the efficiency of employees and improve the quality management of ac plug pcb design products.
A power rating for a PCB, or Printed Circuit Board, is a measure of the maximum amount of power the board is able to safely handle. This rating takes into account the overall design and materials used in the creation of the PCB, as well as the environment in which it will be used. It is an important consideration in electronics and circuit design as exceeding the power rating can lead to overheating and potential damage to the board and connected components. Properly understanding and adhering to the power rating of a PCB is crucial for ensuring safe and efficient operation of electronic devices.
4.What type of material is used for the silkscreen on a ac plug pcb design?
We have a wide range of ac plug pcb design customer groups and establishes long -term cooperative relationships with partners. The countries we provide services include .
The material used for the silkscreen on a PCB is typically a white or black ink made of epoxy or acrylic. It is applied using a screen printing process and is cured at high temperatures to ensure durability and resistance to chemicals and solvents.
5.How are signal integrity issues addressed in ac plug pcb design design?
We focus on our customers' needs and strive to meet their expectations, so we take this very seriously.
Signal integrity issues are a common concern in PCB design, as they can greatly affect the performance and reliability of electronic systems. These issues arise from high-speed signal transmissions on the board, which can result in degraded signals, data errors, and even system failures. In order to address these issues, PCB designers must consider various factors such as layout, routing, and component placement to ensure proper signal integrity. This involves implementing signal protection measures such as controlled impedance routing, signal shielding, and minimizing signal crosstalk. Additionally, designers may use simulation and analysis tools to identify and resolve any potential signal integrity problems before the PCB goes into production. By carefully addressing signal integrity issues in the design phase, PCBs can achieve optimal performance and functionality.
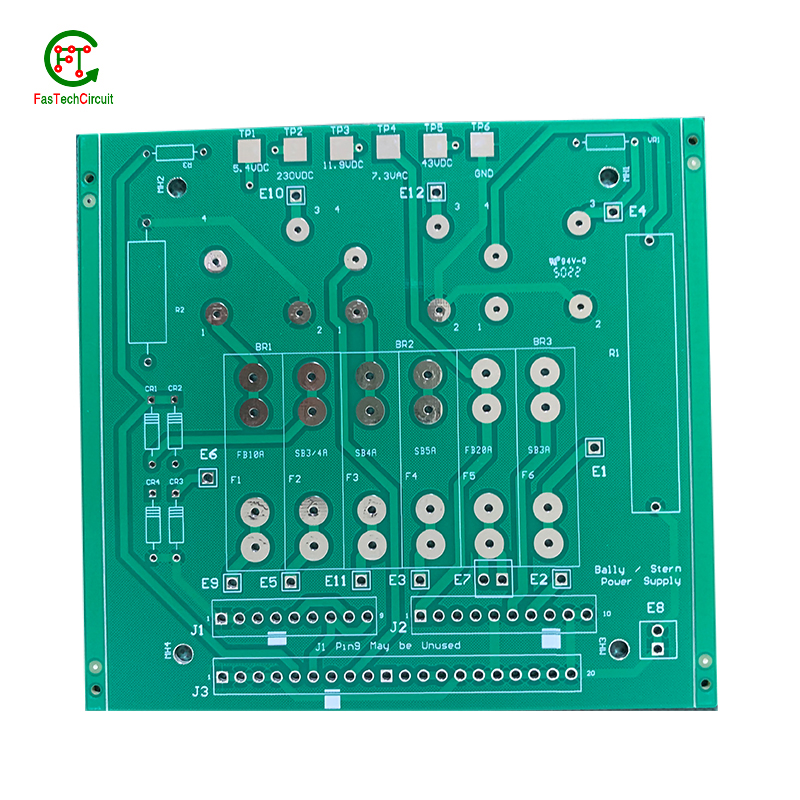
6.What is the difference between a copper pour and a trace on a ac plug pcb design?
We adhere to the principle of quality first and have a complete production quality management system and quality inspection process.
A copper pour and a trace are two common electronic components that are found on a printed circuit board (PCB). A copper pour is a large area of copper that is used to connect multiple components or ground signals together on a PCB. This creates a solid and low resistance pathway for signals to flow. On the other hand, a trace is a thin line of copper used to connect individual components on a PCB. It carries a specific signal from one component to another. Unlike a copper pour, a trace can be designed to carry a specific current and have a specific width to meet the requirements of the circuit.
7.What techniques are used for reducing electromagnetic interference (EMI) on a ac plug pcb design?
Electromagnetic interference (EMI) is a disturbance caused by electromagnetic radiation that can disrupt the proper functioning of electronic devices. To reduce EMI on a PCB, a number of techniques can be employed. One common technique is to use a ground plane, which acts as a shield to block electromagnetic waves from interfering with the circuit. Another approach is to use proper placement and routing of components and traces to minimize the length of signal paths and reduce the chances of signal crossover. Additionally, using components like capacitors and ferrite beads can help to filter out high-frequency noise. Careful consideration and design of the PCB layout is also crucial in reducing EMI, as the placement, size, and orientation of components can impact electromagnetic emissions. By employing these techniques, EMI on a PCB can be effectively reduced, leading to improved performance and reliability of electronic devices.
8.What are the main components of a ac plug pcb design?
We continuously upgrade our skills and knowledge to adapt to changing ac plug pcb design market needs.
A typical PCB consists of several vital components, including a substrate material, copper traces, solder mask, silk screen, and plated through-holes. The substrate material acts as the base and provides mechanical support for the board. Copper traces, usually made of thin lines of copper foil, serve as the conductive paths for transmitting electrical signals. The solder mask, applied as a protective layer, prevents accidental short circuits and corrosion. Silk screen, a layer of ink-based labeling, aids in component identification. Lastly, plated through-holes enable electrical connection between different layers of the PCB board. These components work together to form a fully functioning PCB.
9.What is the purpose of a ground plane on a ac plug pcb design?
I have a comprehensive after -sales service system, which can pay attention to market trends in time and adjust our strategy in a timely manner.
A decoupling capacitor is an essential component on a PCB (Printed Circuit Board) which is used to reduce or eliminate high frequency noise between different components. It acts as a buffer between the power supply and other circuit components, by storing electrical charge and then releasing it when there is a sudden change in the supply voltage. This helps to stabilize the power supply, providing a steady and noise-free flow of electricity to the circuit. Furthermore, decoupling capacitors also help to filter out any unwanted signals that may cause interference or disruptions in the proper functioning of the circuit.
10.What materials are used to make a ac plug pcb design?
We have advanced production equipment and technology to meet the needs of customers, and can provide customers with high quality, low priced ac plug pcb design products.
A PCB, or printed circuit board, is typically made of a non-conductive material such as fiberglass or composite epoxy resin. This material acts as a base for a thin layer of copper foil, which is then etched to create the desired circuit pattern. Other common materials used in the production of PCBs include solder mask, a polymer layer used to insulate and protect the copper traces, and silkscreen, which is used to label and identify the different components on the PCB. In addition, various electronic components such as resistors, capacitors, and diodes are also mounted onto the PCB to form a functional electronic circuit. Other potential materials used in the production of PCBs include metal core, ceramics, and conductive ink, depending on the specific design and requirements of the circuit.
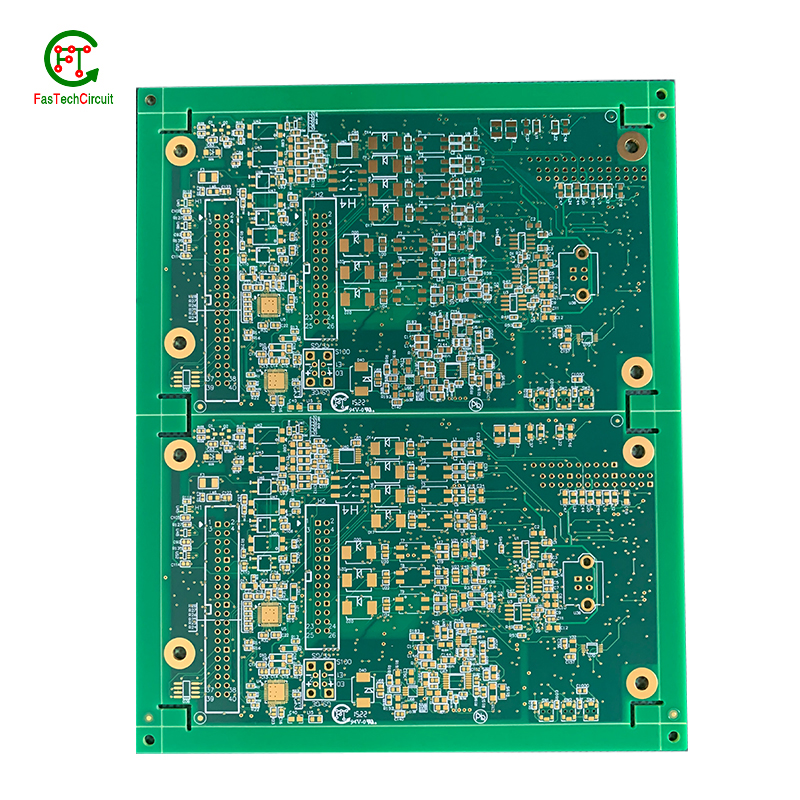
11.What is the minimum size of a through-hole component that can be used on a ac plug pcb design?
We continue to invest in research and development and continue to launch innovative products.
The minimum size of a through-hole component that can be used on a PCB depends on the capabilities of the PCB manufacturer and the design requirements of the circuit. Generally, the minimum size for a through-hole component is around 0.2mm in diameter, but some manufacturers may be able to produce smaller sizes. It is important to consult with the manufacturer and consider the design requirements to determine the appropriate size for a through-hole component on a PCB.
12.Can a ac plug pcb design be repaired if damaged?
We focus on teamwork and communication to achieve common goals, We attach great importance to this detail.
Yes, a PCB (printed circuit board) can be repaired if it is damaged. The extent of the damage and the complexity of the circuit will determine the difficulty and feasibility of the repair. Some common methods for repairing a damaged PCB include:
1. Soldering: If the damage is limited to a few components or traces, they can be replaced or repaired by soldering new components or wires onto the board.
2. Trace repair: If a trace (conductive pathway) on the PCB is damaged or broken, it can be repaired by using a conductive ink or wire to bridge the gap.
3. Component replacement: If a specific component on the PCB is damaged, it can be replaced with a new one. This requires identifying the damaged component and sourcing a replacement.
4. PCB rework: In some cases, the entire PCB may need to be reworked, which involves removing and replacing multiple components and traces.
13.What is the maximum size of a ac plug pcb design?
We pay attention to the introduction and training of talents, scientifically regulate the management system, and focus on cultural construction and team cohesion.
The maximum size of a PCB (printed circuit board) can vary depending on the manufacturer and theircapabilities. However, the industry standard maximum size for a single PCB panel is typically around 18 inches by 24 inches (457 mm by 610 mm). Larger PCBs can be created by combining multiple panels together. Some manufacturers may also have the capability to create custom-sized PCBs that exceed the industry standard maximum size.
14.What is the role of automated optical inspection (AOI) in ac plug pcb design production?
Automated optical inspection (AOI) plays a crucial role in the production of printed circuit boards (PCBs). It is a technology that uses advanced imaging techniques to detect and identify defects or errors on a PCB, such as missing components, incorrect placement, and faulty soldering. AOI has become an essential step in the production process as it helps manufacturers ensure the quality and reliability of their PCBs. By detecting and identifying defects at an early stage, AOI can significantly reduce the number of defects and increase the efficiency of the production process. Furthermore, AOI is able to perform inspections at a much faster rate and with higher accuracy compared to manual inspection, making it an indispensable tool for PCB production.
15.What types of ac plug pcb designs are there?
As one of the ac plug pcb design market leaders, we are known for innovation and reliability.
There are several types of PCBs, including single-sided, double-sided, multi-layer, and flexible PCBs. Single-sided PCBs have components mounted on one side and conductive traces on the other. Double-sided PCBs have components mounted on both sides with conductive traces connecting them. Multi-layer PCBs have several layers of conductive traces and insulating material sandwiched together. Flexible PCBs are made from a flexible plastic material, allowing them to bend and twist for use in applications where traditional rigid PCBs are not suitable. Each type of PCB serves a different purpose and can be used in a variety of electronic devices and applications.
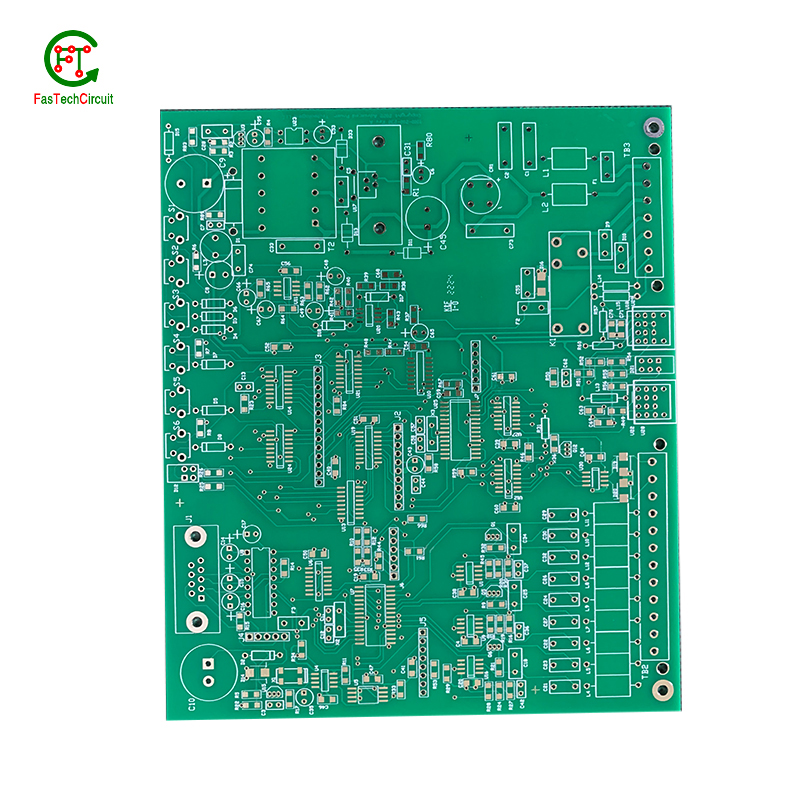
RELATED PRODUCTS & SERVICE
pcb board manufacturing How To Contact US
PCB from 1 to 30 layers, HDI, Heavy Copper, Rigid-flex board with "pcb board manufacturing One-Stop" service.