2018 automated pcb design
Our managers and technicians are all experienced personnel who have been engaged in the PCB industry for more than 20 years, so we have rich production management experience and professional PCB skills. We constantly introduce new equipment, new technologies, and use high-quality materials to ensure the quality of PCB products. We have professional technical personnel who can provide early design consultation and technical support, making customers more worry-free. With high-quality and reliable products, advanced technology and value-added services, our products are very popular in United Kingdom,Holy See (Vatican City),Pakistan,Coral Sea Islands,Fiji, the United States and Japan. Won high praise from customers.
Base Material | FR-4/CEM-1/CEM-3/Polyimild/PTFE/Rogers |
Board Thickness | 0.2-8mm |
Model Number | Custom PCB & PCB Assembly |
Type | Aluminum PCB |
Brand Name | FC |
Copper Thickness | 0.3-2mil(10-51um) |
Min. Hole Size | 0.1mm(4mil)for HDI / 0.15mm(6mil) |
Min. Line Width | 0.075mm/0.075mm(3mil/3mil) |
Min. Line Spacing | 0.003'' |
Surface Finishing | HASL/OSP/Ag/ENIG/ENEPIG/Immersion silver/Tin |
Board Size | Custom |
Model Number | Customized |
Base Material | FR4 Aluminum CEM-1 94V0 |
Surface Finishing | HASLENIG OSP |
Number of layer | 1-16layer |
Other service | Components purchasing and assem |
ly Solder mask | White Black Green Blue,Red,etc. |
Dsign service | Available |
Testing | Function testing |
Certificate | RoHS, ISO/TS16949, ISO9001 |
Name | High Quality led light aluminum pcb printed circuit board |
Packaging Details | Vaccum package and standard carton outside High Quality led light aluminum pcb printed circuit board |
Supply Ability | 51630 Square Meter/Square Meters per Month |
Quantity (pieces) | > 17866 |
Lead time (days) | 7 |
2018 automated pcb design bearings FAQs Guide Welcome to our state-of-the-art PCB (Printed Circuit Board) products. We are proud to offer a comprehensive range of high-quality and versatile PCB solutions to meet the constantly evolving needs of the modern electronics industry.Our PCBs are expertly designed and manufactured using the latest technology and advanced techniques, ensuring reliability, durability, and exceptional performance for a wide range of applications. We understand the importance of precision and attention to detail in the production of PCBs and we are committed to meeting stringent quality standards.
2.What are the advantages of using a 2018 automated pcb design?
3.What are the main components of a 2018 automated pcb design?
4.What type of material is used for the silkscreen on a 2018 automated pcb design?
5.How are components selected for a 2018 automated pcb design design?
6.What is the minimum trace width and spacing on a 2018 automated pcb design?
7.What are some common 2018 automated pcb design layout guidelines?
8.Can a 2018 automated pcb design be used for both power and signal transmission?
9.How are high-speed/high-frequency 2018 automated pcb design tested and validated?
10.How are 2018 automated pcb design used in medical devices?
11.What does 2018 automated pcb design stand for?
12.What is the minimum size of a through-hole component that can be used on a 2018 automated pcb design?
13.What is the role of silkscreen on a 2018 automated pcb design?
14.What is the function of a decoupling capacitor on a 2018 automated pcb design?
15.What is the role of vias on a 2018 automated pcb design?
16.What is the typical lifespan of a 2018 automated pcb design?
17.Are 2018 automated pcb design recyclable?
1.What is the process of etching a 2018 automated pcb design?
We have flexible production capacity. Whether you are large orders or small orders, you can produce and release goods in a timely manner to meet customer needs.
PCB (Printed Circuit Board) etching is the process of creating a circuit pattern on a copper-clad board by using chemical etchants to selectively remove the unwanted copper. The process begins by transferring the circuit design onto a copper-clad board using various methods such as printing or photolithography. Next, the board is coated with a resist material, which protects the areas of copper that will eventually become the circuit traces. The board is then placed in an etching solution, typically a mixture of acid and water, which dissolves the unprotected copper. Once the desired circuit pattern is etched into the board, the resist material is removed, and the board is cleaned and inspected for any imperfections. PCB etching is a crucial step in the manufacturing of PCBs, as it creates the necessary conductive pathways for electronic components to be mounted and interconnected, making it an essential process in the production of electronic devices.
2.What are the advantages of using a 2018 automated pcb design?
We are centered on customers and always pay attention to customers' needs for 2018 automated pcb design products.
There are several advantages of using a PCB (Printed Circuit Board). Firstly, a PCB provides a compact and organized layout for electronic components, which makes it easier for technicians to troubleshoot and repair any issues. Secondly, it reduces the chances of loose connections and short circuits, which can be a major safety concern. Thirdly, PCBs are cost-effective and can be easily mass-produced, making them a popular choice for large-scale production. Additionally, they offer durability and stability, ensuring long-lasting performance. Finally, PCBs also allow for easy integration of new components, making it easier to upgrade or modify the electronic devices.
3.What are the main components of a 2018 automated pcb design?
We continuously upgrade our skills and knowledge to adapt to changing 2018 automated pcb design market needs.
A typical PCB consists of several vital components, including a substrate material, copper traces, solder mask, silk screen, and plated through-holes. The substrate material acts as the base and provides mechanical support for the board. Copper traces, usually made of thin lines of copper foil, serve as the conductive paths for transmitting electrical signals. The solder mask, applied as a protective layer, prevents accidental short circuits and corrosion. Silk screen, a layer of ink-based labeling, aids in component identification. Lastly, plated through-holes enable electrical connection between different layers of the PCB board. These components work together to form a fully functioning PCB.
4.What type of material is used for the silkscreen on a 2018 automated pcb design?
We have a wide range of 2018 automated pcb design customer groups and establishes long -term cooperative relationships with partners. The countries we provide services include .
The material used for the silkscreen on a PCB is typically a white or black ink made of epoxy or acrylic. It is applied using a screen printing process and is cured at high temperatures to ensure durability and resistance to chemicals and solvents.
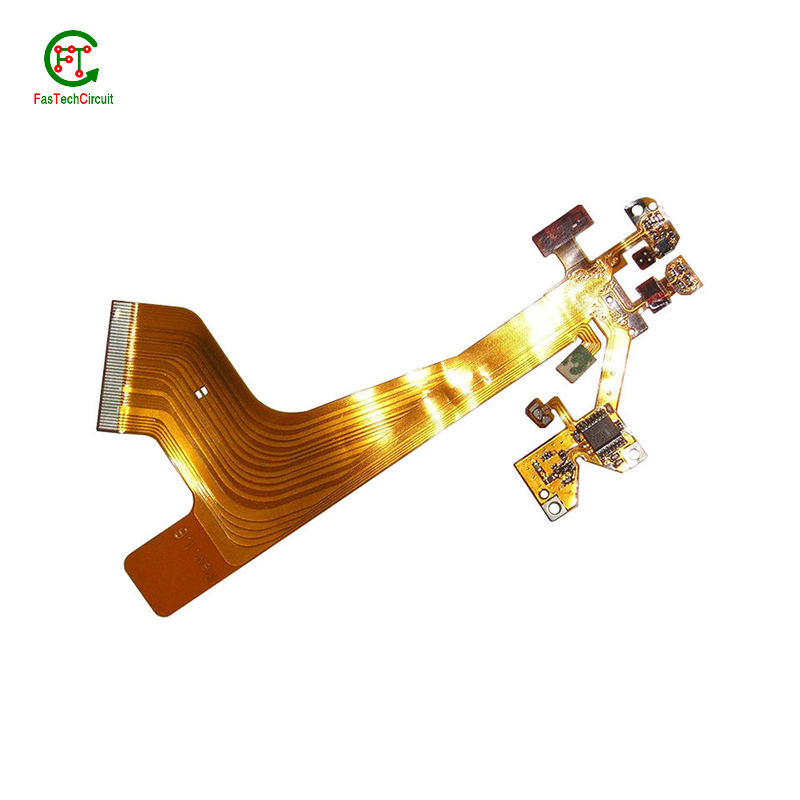
5.How are components selected for a 2018 automated pcb design design?
We pay attention to employee development and benefits, and provide a good working environment in order to improve the efficiency of employees and improve the quality management of 2018 automated pcb design products.
A power rating for a PCB, or Printed Circuit Board, is a measure of the maximum amount of power the board is able to safely handle. This rating takes into account the overall design and materials used in the creation of the PCB, as well as the environment in which it will be used. It is an important consideration in electronics and circuit design as exceeding the power rating can lead to overheating and potential damage to the board and connected components. Properly understanding and adhering to the power rating of a PCB is crucial for ensuring safe and efficient operation of electronic devices.
6.What is the minimum trace width and spacing on a 2018 automated pcb design?
We operate our 2018 automated pcb design business with integrity and honesty.
The minimum trace width and spacing on a PCB can vary depending on the manufacturing process and the specific requirements of the design. However, a common industry standard for minimum trace width and spacing is 0.006 inches (0.1524 mm). This is typically used for standard PCBs with a 1 oz copper weight. For more complex designs or higher copper weights, the minimum trace width and spacing may need to be increased to ensure proper functionality and reliability. It is important to consult with the PCB manufacturer and follow their guidelines for minimum trace width and spacing to ensure a successful design.
7.What are some common 2018 automated pcb design layout guidelines?
We should have a stable supply chain and logistics capabilities, and provide customers with high -quality, low -priced 2018 automated pcb design products.
Thermal considerations play a crucial role in the design of printed circuit boards (PCBs). The concept of heat management is critical as excessive heat can lead to reduced performance and potential damage to the electronic components on the board. This is why thermal considerations are carefully taken into account during PCB design. Designers must carefully consider factors such as the size, placement, and orientation of components on the board to ensure efficient heat dissipation. They also need to factor in the type and thickness of the board material, as well as incorporate proper ventilation and heat sinks to prevent overheating. By carefully considering these thermal aspects during the design process, the resulting PCBs can perform optimally and have a longer lifespan.
8.Can a 2018 automated pcb design be used for both power and signal transmission?
Yes, a PCB (printed circuit board) can be used for both power and signal transmission. This is commonly seen in electronic devices such as computers, smartphones, and other electronic devices. The PCB acts as a platform for connecting various components and circuits, including power sources and signal pathways. The power and signal traces on the PCB are designed to handle different levels of current and voltage to ensure efficient transmission and prevent interference between the two. However, it is important to properly design and layout the PCB to ensure proper separation and isolation of power and signal traces to avoid any potential issues.
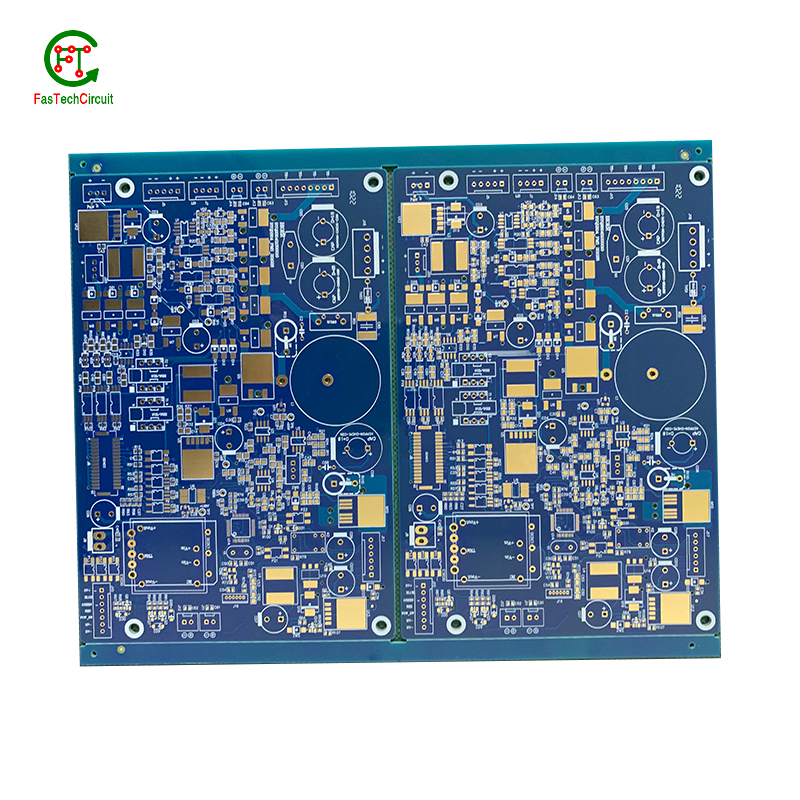
9.How are high-speed/high-frequency 2018 automated pcb design tested and validated?
Testing and validation are essential steps in the production process of high-speed and high-frequency printed circuit boards (PCBs). These specialized types of PCBs are used in a wide range of industries, including telecommunications, aerospace, and automotive, and require precision and reliability in their performance.
The testing and validation process for high-speed/high-frequency PCBs involves several steps to ensure that the final product meets the required specifications. This starts with design simulation and analysis using specialized software to verify the layout and electrical characteristics of the PCB.
Once the design is confirmed, prototype PCBs are manufactured and subjected to various tests, including signal integrity and power integrity tests. These tests evaluate the electrical performance of the PCB, such as its ability to transmit signals at high speeds and maintain signal integrity.
In addition to electrical tests, environmental and mechanical tests are also performed to assess the durability and reliability of the PCB under different conditions, such as temperature changes and mechanical stress.
The final step in the testing and validation process is the inspection and analysis of the tested PCBs. This involves a detailed review of the test results and any necessary modifications to meet the required specifications.
10.How are 2018 automated pcb design used in medical devices?
Printed Circuit Boards (PCBs) are essential components used in a wide range of medical devices, playing a crucial role in both diagnostic and treatment equipment. These devices require reliable and precise circuitry to accurately collect and process data, deliver therapies, and regulate medical procedures. PCBs are used in equipment such as MRI machines, pacemakers, defibrillators, and monitors, where their small size and high density make them ideal for compact and portable designs. In addition, PCBs are also used in medical implants, enabling a safe and secure connection between the device and the body. With their advanced technology, PCBs continue to be an integral part of the medical industry, ensuring the effectiveness and success of various medical procedures and treatments.
11.What does 2018 automated pcb design stand for?
We attach importance to the innovation ability and team spirit of employees, have advanced R & D facilities and laboratories, and have a good quality management system.
PCB stands for Printed Circuit Board.
12.What is the minimum size of a through-hole component that can be used on a 2018 automated pcb design?
We continue to invest in research and development and continue to launch innovative products.
The minimum size of a through-hole component that can be used on a PCB depends on the capabilities of the PCB manufacturer and the design requirements of the circuit. Generally, the minimum size for a through-hole component is around 0.2mm in diameter, but some manufacturers may be able to produce smaller sizes. It is important to consult with the manufacturer and consider the design requirements to determine the appropriate size for a through-hole component on a PCB.
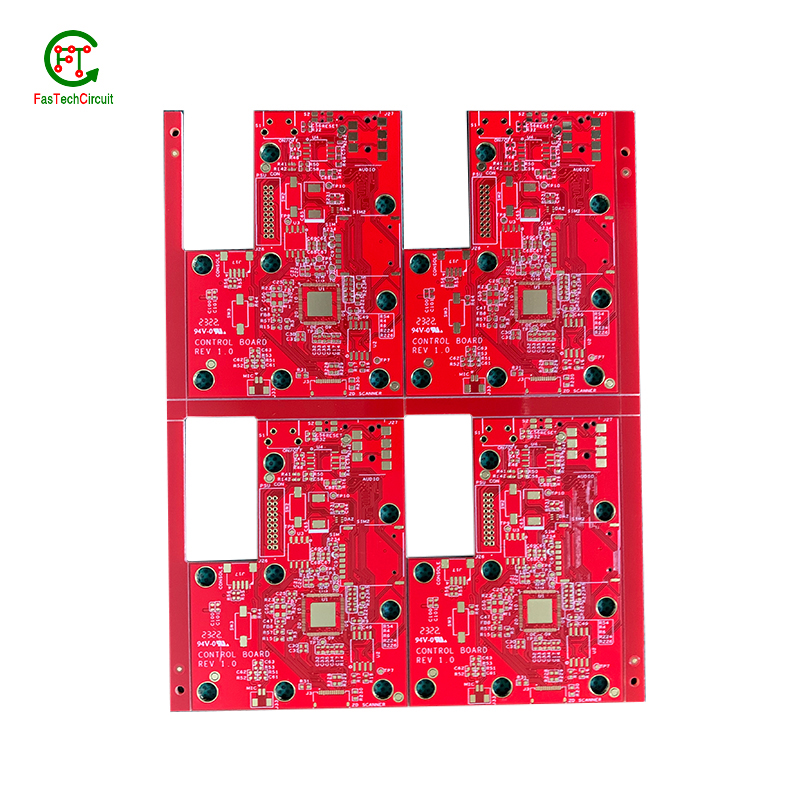
13.What is the role of silkscreen on a 2018 automated pcb design?
Being one of the top 2018 automated pcb design manufacturers in China, We attach great importance to this detail.
Silkscreen, also known as legend or nomenclature, is a vital component of a printed circuit board (PCB). It is the layer of text and symbols that are printed on the surface of the PCB to provide essential information for component placement and identification. The silkscreen plays a crucial role in the manufacturing process of PCBs, as it helps to ensure the accuracy and functionality of the final product. By indicating component locations, values, and reference designators, the silkscreen serves as a guide for the assembly and soldering of electronic components. Additionally, it also provides important information for maintenance and troubleshooting purposes.
14.What is the function of a decoupling capacitor on a 2018 automated pcb design?
We have rich industry experience and professional knowledge, and have strong competitiveness in the market.
A decoupling capacitor is a type of capacitor that is used to reduce or eliminate noise and interference in electronic circuits. It is typically placed on a PCB (printed circuit board) near the power supply pins of an integrated circuit (IC) or other active component.
The main function of a decoupling capacitor is to provide a stable and clean power supply to the IC or other active component. This is achieved by filtering out high-frequency noise and voltage fluctuations that can be caused by other components on the PCB or external sources.
In addition, a decoupling capacitor also helps to prevent voltage drops and spikes that can occur when the IC or other component suddenly draws a large amount of current. This is especially important for sensitive components that require a stable power supply to function properly.
15.What is the role of vias on a 2018 automated pcb design?
Our company has many years of 2018 automated pcb design experience and expertise.
Vias play a crucial role in connecting different layers of a printed circuit board (PCB). These small, plated holes act as conductive paths, allowing signals and power to pass through the board and reach various components. Vias are also essential for routing traces from one layer to another, optimizing the layout and reducing the size and complexity of the board. Additionally, vias provide structural support and improve thermal management by facilitating heat dissipation.
16.What is the typical lifespan of a 2018 automated pcb design?
2018 automated pcb design is not a product only, but also can help you comes to money-making.
The typical lifespan of a PCB (printed circuit board) can vary greatly depending on various factors such as the quality of materials used, environmental conditions, and usage. In general, a well-designed and properly manufactured PCB can last for 10-20 years or more. However, some PCBs may fail prematurely due to factors such as corrosion, thermal stress, or mechanical damage. Regular maintenance and proper handling can also extend the lifespan of a PCB.
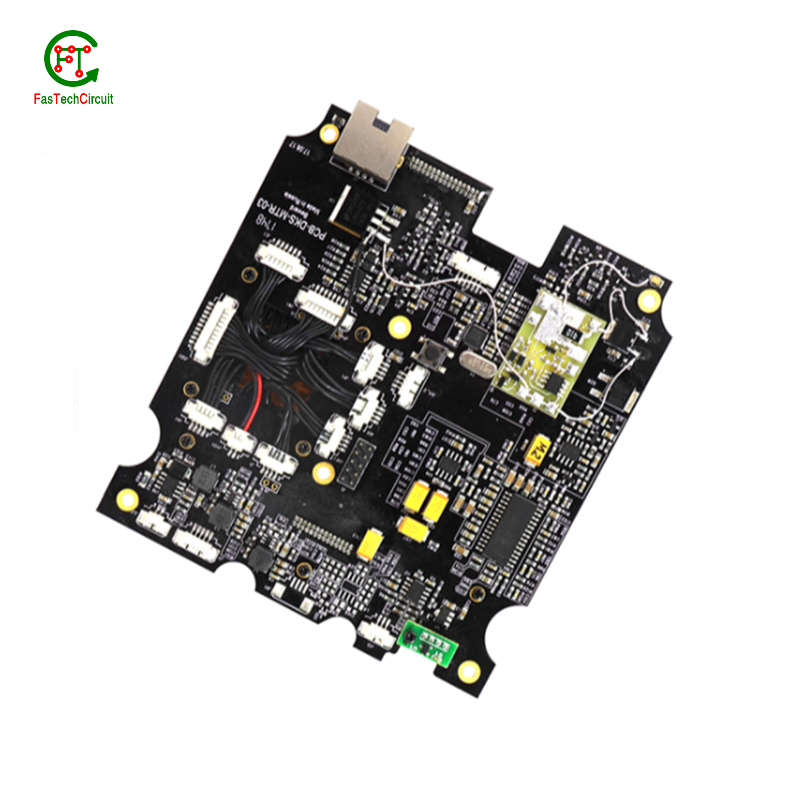
17.Are 2018 automated pcb design recyclable?
We have been working hard to improve service quality and meet customer needs.
Yes, PCBs (printed circuit boards) are recyclable. They can be broken down and the individual components can be reused or repurposed. However, the recycling process can be complex and requires specialized equipment and techniques. It is important to properly dispose of PCBs to prevent environmental contamination and health hazards.
RELATED PRODUCTS & SERVICE
pcb board manufacturing How To Contact US
PCB from 1 to 30 layers, HDI, Heavy Copper, Rigid-flex board with "pcb board manufacturing One-Stop" service.