3s pcb battery protection board
Our managers and technicians are all experienced personnel who have been engaged in the PCB industry for more than 20 years, so we have rich production management experience and professional PCB skills. We constantly introduce new equipment, new technologies, and use high-quality materials to ensure the quality of PCB products. We have professional technical personnel who can provide early design consultation and technical support, making customers more worry-free. With high-quality and reliable products, advanced technology and value-added services, our products are very popular in Andorra,Germany,Sierra Leone, the United States and Japan. Won high praise from customers.
Base Material | FR-4/CEM-1/CEM-3/Polyimild/PTFE/Rogers |
Board Thickness | 0.1-6mm |
Model Number | Custom PCB & PCB Assembly |
Type | Aluminum PCB |
Brand Name | FC |
Copper Thickness | 0.2-2mil(8-52um) |
Min. Hole Size | 0.1mm(4mil)for HDI / 0.15mm(6mil) |
Min. Line Width | 0.075mm/0.075mm(3mil/3mil) |
Min. Line Spacing | 0.003'' |
Surface Finishing | HASL/OSP/Ag/ENIG/ENEPIG/Immersion silver/Tin |
Board Size | Custom |
Model Number | Customized |
Base Material | FR4 Aluminum CEM-1 94V0 |
Surface Finishing | HASLENIG OSP |
Number of layer | 1-16layer |
Other service | Components purchasing and assem |
ly Solder mask | White Black Green Blue,Red,etc. |
Dsign service | Available |
Testing | Function testing |
Certificate | RoHS, ISO/TS16949, ISO9001 |
Name | High Quality led light aluminum pcb printed circuit board |
Packaging Details | Vaccum package and standard carton outside High Quality led light aluminum pcb printed circuit board |
Supply Ability | 42365 Square Meter/Square Meters per Month |
Quantity (pieces) | > 19193 |
Lead time (days) | 12 |
3s pcb battery protection board bearings FAQs Guide Welcome to our state-of-the-art PCB (Printed Circuit Board) products. We are proud to offer a comprehensive range of high-quality and versatile PCB solutions to meet the constantly evolving needs of the modern electronics industry.Our PCBs are expertly designed and manufactured using the latest technology and advanced techniques, ensuring reliability, durability, and exceptional performance for a wide range of applications. We understand the importance of precision and attention to detail in the production of PCBs and we are committed to meeting stringent quality standards.
2.What techniques are used for reducing electromagnetic interference (EMI) on a 3s pcb battery protection board?
3.Can a 3s pcb battery protection board be used with both through-hole and surface mount components?
4.Are 3s pcb battery protection board recyclable?
5.What is the role of automated optical inspection (AOI) in 3s pcb battery protection board production?
6.What are some common problems that can occur with 3s pcb battery protection board?
7.What is the power rating for a 3s pcb battery protection board?
8.What is embedded 3s pcb battery protection board technology?
9.What is the minimum trace width and spacing on a 3s pcb battery protection board?
10.How are components selected for a 3s pcb battery protection board design?
11.What is the purpose of a 3s pcb battery protection board?
12.What materials are used to make a 3s pcb battery protection board?
13.What is the difference between a gold-plated and a tin-plated 3s pcb battery protection board?
14.What is a through-hole component?
15.How are 3s pcb battery protection boards designed?
16.What is the purpose of a solder mask on a 3s pcb battery protection board?
17.Can 3s pcb battery protection boards be used in high voltage applications?
18.How are high-speed/high-frequency 3s pcb battery protection board tested and validated?
1.What are some common 3s pcb battery protection board layout guidelines?
We should have a stable supply chain and logistics capabilities, and provide customers with high -quality, low -priced 3s pcb battery protection board products.
Thermal considerations play a crucial role in the design of printed circuit boards (PCBs). The concept of heat management is critical as excessive heat can lead to reduced performance and potential damage to the electronic components on the board. This is why thermal considerations are carefully taken into account during PCB design. Designers must carefully consider factors such as the size, placement, and orientation of components on the board to ensure efficient heat dissipation. They also need to factor in the type and thickness of the board material, as well as incorporate proper ventilation and heat sinks to prevent overheating. By carefully considering these thermal aspects during the design process, the resulting PCBs can perform optimally and have a longer lifespan.
2.What techniques are used for reducing electromagnetic interference (EMI) on a 3s pcb battery protection board?
Electromagnetic interference (EMI) is a disturbance caused by electromagnetic radiation that can disrupt the proper functioning of electronic devices. To reduce EMI on a PCB, a number of techniques can be employed. One common technique is to use a ground plane, which acts as a shield to block electromagnetic waves from interfering with the circuit. Another approach is to use proper placement and routing of components and traces to minimize the length of signal paths and reduce the chances of signal crossover. Additionally, using components like capacitors and ferrite beads can help to filter out high-frequency noise. Careful consideration and design of the PCB layout is also crucial in reducing EMI, as the placement, size, and orientation of components can impact electromagnetic emissions. By employing these techniques, EMI on a PCB can be effectively reduced, leading to improved performance and reliability of electronic devices.
3.Can a 3s pcb battery protection board be used with both through-hole and surface mount components?
We continue to improve 3s pcb battery protection board products and processes to improve efficiency.
Yes, a PCB (printed circuit board) can be designed to accommodate both through-hole and surface mount components. This is known as a mixed-technology PCB. The PCB will have both through-hole and surface mount pads and traces, allowing for the placement and soldering of both types of components. This type of PCB is commonly used in electronic devices that require a combination of through-hole and surface mount components for functionality.
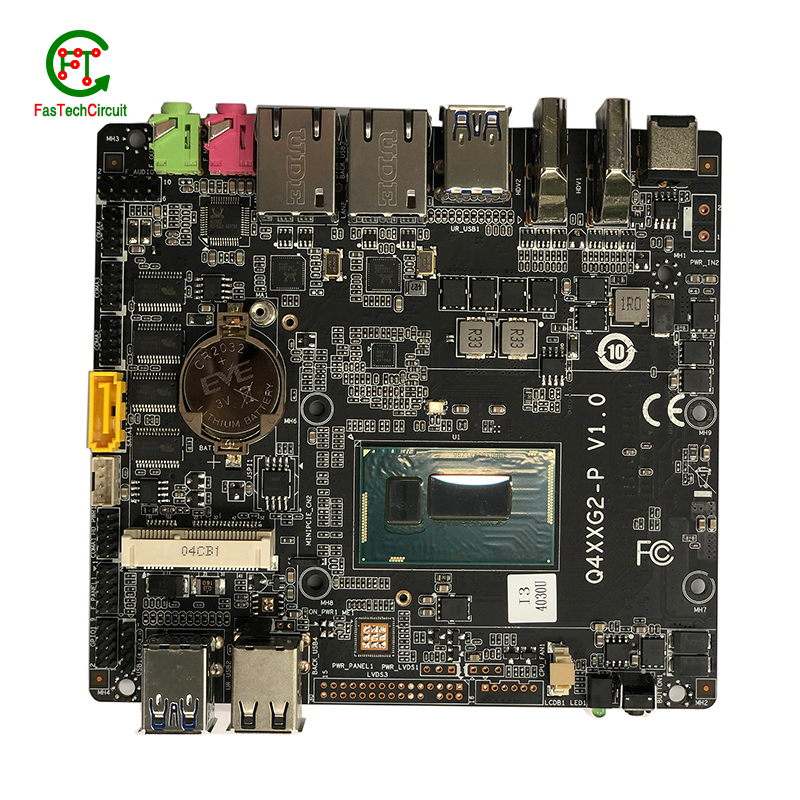
4.Are 3s pcb battery protection board recyclable?
We have been working hard to improve service quality and meet customer needs.
Yes, PCBs (printed circuit boards) are recyclable. They can be broken down and the individual components can be reused or repurposed. However, the recycling process can be complex and requires specialized equipment and techniques. It is important to properly dispose of PCBs to prevent environmental contamination and health hazards.
5.What is the role of automated optical inspection (AOI) in 3s pcb battery protection board production?
Automated optical inspection (AOI) plays a crucial role in the production of printed circuit boards (PCBs). It is a technology that uses advanced imaging techniques to detect and identify defects or errors on a PCB, such as missing components, incorrect placement, and faulty soldering. AOI has become an essential step in the production process as it helps manufacturers ensure the quality and reliability of their PCBs. By detecting and identifying defects at an early stage, AOI can significantly reduce the number of defects and increase the efficiency of the production process. Furthermore, AOI is able to perform inspections at a much faster rate and with higher accuracy compared to manual inspection, making it an indispensable tool for PCB production.
6.What are some common problems that can occur with 3s pcb battery protection board?
Our 3s pcb battery protection board products undergo strict quality control to ensure customer satisfaction.
PCB (printed circuit boards) are an integral part of electronic devices, serving as the foundation for electrical connections and components. However, like any other technology, there are certain issues that may arise with PCB. One common problem is damage to the board due to excessive heat, as electronic components generate heat and if the PCB is not properly designed or ventilated, it can lead to malfunctions or even permanent damage. Another issue is poor soldering, which can result in weak connections or no connection at all. This can be caused by inadequate equipment or inexperience in the assembly process. Additionally, PCB can also suffer from corrosion over time, especially in high humidity environments, affecting its performance and reliability. It is important to address these problems early on to prevent further damage and ensure the functionality of electronic devices. Regular maintenance, proper design and assembly techniques, and use of quality materials can help prevent these common issues with PCB.
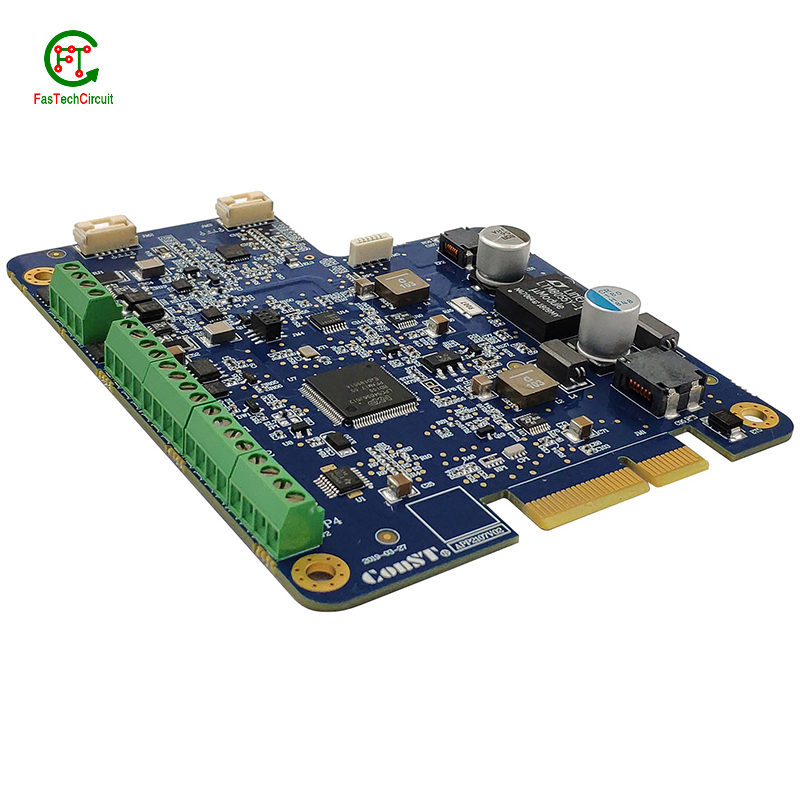
7.What is the power rating for a 3s pcb battery protection board?
We maintain a certain amount of R&D investment every year and continuously improve operational efficiency to provide better services to our cooperative customers.
The power rating for a PCB (printed circuit board) can vary greatly depending on its size, design, and intended use. Generally, the power rating for a PCB is determined by the maximum amount of current it can safely handle without overheating or causing damage. This can range from a few milliamps for small, low-power circuits to several amps for larger, high-power circuits. It is important to consult the manufacturer's specifications or consult with an engineer to determine the specific power rating for a particular PCB.
8.What is embedded 3s pcb battery protection board technology?
Our products & services cover a wide range of areas and meet the needs of different fields.
Embedded PCB technology refers to the integration of electronic components directly onto a printed circuit board (PCB) during the manufacturing process. This allows for a more compact and efficient design, as well as improved reliability and performance. The components are embedded within the layers of the PCB, rather than being mounted on the surface, resulting in a more streamlined and durable product. This technology is commonly used in applications such as smartphones, tablets, and other portable electronic devices.
9.What is the minimum trace width and spacing on a 3s pcb battery protection board?
We operate our 3s pcb battery protection board business with integrity and honesty.
The minimum trace width and spacing on a PCB can vary depending on the manufacturing process and the specific requirements of the design. However, a common industry standard for minimum trace width and spacing is 0.006 inches (0.1524 mm). This is typically used for standard PCBs with a 1 oz copper weight. For more complex designs or higher copper weights, the minimum trace width and spacing may need to be increased to ensure proper functionality and reliability. It is important to consult with the PCB manufacturer and follow their guidelines for minimum trace width and spacing to ensure a successful design.
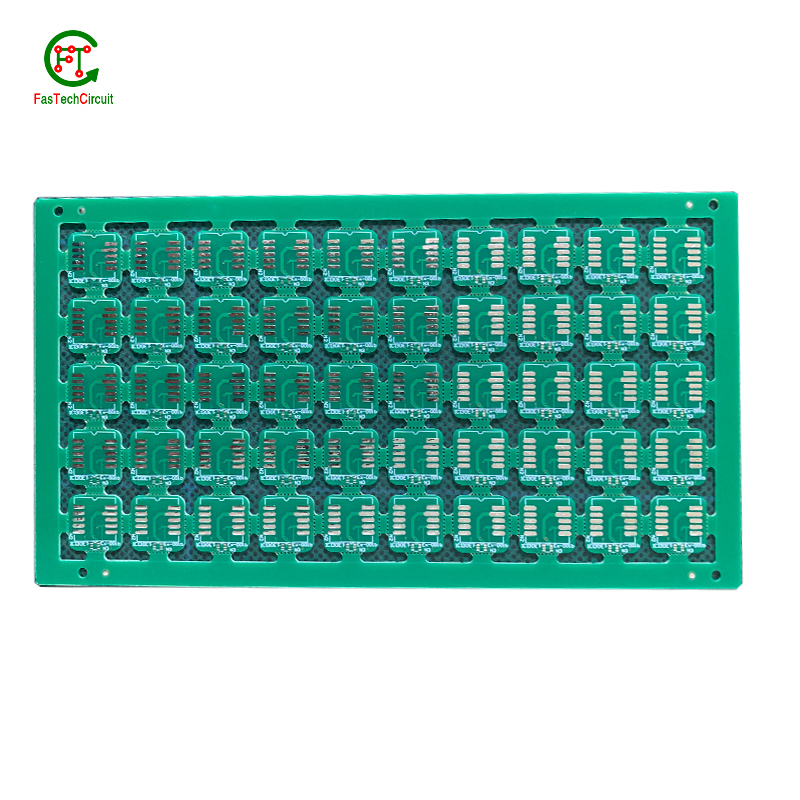
10.How are components selected for a 3s pcb battery protection board design?
We pay attention to employee development and benefits, and provide a good working environment in order to improve the efficiency of employees and improve the quality management of 3s pcb battery protection board products.
A power rating for a PCB, or Printed Circuit Board, is a measure of the maximum amount of power the board is able to safely handle. This rating takes into account the overall design and materials used in the creation of the PCB, as well as the environment in which it will be used. It is an important consideration in electronics and circuit design as exceeding the power rating can lead to overheating and potential damage to the board and connected components. Properly understanding and adhering to the power rating of a PCB is crucial for ensuring safe and efficient operation of electronic devices.
11.What is the purpose of a 3s pcb battery protection board?
We pay attention to the transformation of intellectual property protection and innovation achievements. Your OEM or ODM order design we have a complete confidentiality system.
A PCB (Printed Circuit Board) is a flat board made of non-conductive material, such as fiberglass, with conductive pathways etched or printed onto it. The main purpose of a PCB is to provide a platform for electronic components to be mounted and connected together to form a functioning electronic circuit. It serves as a physical support for the components and provides a means for them to communicate with each other through the conductive pathways. PCBs are used in a wide range of electronic devices, from simple household appliances to complex computer systems, and are essential for the proper functioning and reliability of these devices. They also allow for easier and more efficient production of electronic devices, as the components can be mounted and connected in a standardized and automated manner.
12.What materials are used to make a 3s pcb battery protection board?
We have advanced production equipment and technology to meet the needs of customers, and can provide customers with high quality, low priced 3s pcb battery protection board products.
A PCB, or printed circuit board, is typically made of a non-conductive material such as fiberglass or composite epoxy resin. This material acts as a base for a thin layer of copper foil, which is then etched to create the desired circuit pattern. Other common materials used in the production of PCBs include solder mask, a polymer layer used to insulate and protect the copper traces, and silkscreen, which is used to label and identify the different components on the PCB. In addition, various electronic components such as resistors, capacitors, and diodes are also mounted onto the PCB to form a functional electronic circuit. Other potential materials used in the production of PCBs include metal core, ceramics, and conductive ink, depending on the specific design and requirements of the circuit.
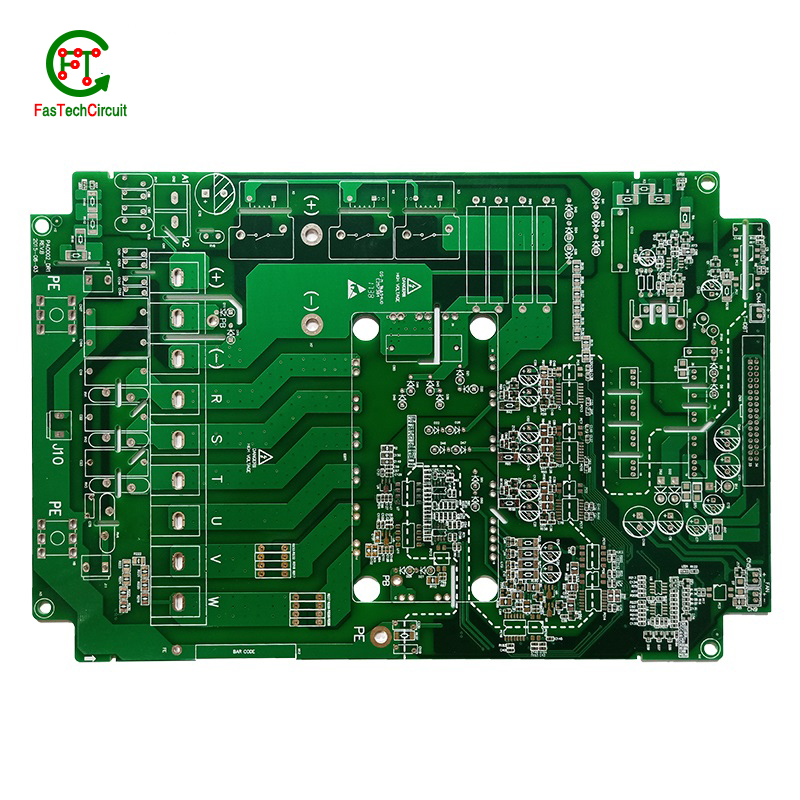
13.What is the difference between a gold-plated and a tin-plated 3s pcb battery protection board?
A gold-plated PCB (Printed Circuit Board) is a type of PCB that has a thin layer of gold coating on its surface. This layer is added through a process called electroplating and is commonly used to protect the PCB components from corrosion and increase the conductivity. On the other hand, a tin-plated PCB has a layer of tin coating on its surface, which is also applied through electroplating. Unlike gold plating, tin plating is mainly used to prevent oxidization and improve solderability.
14.What is a through-hole component?
We focus on providing high 3s pcb battery protection board quality products and services.
A through-hole component is an electronic component that has leads or pins that are inserted into holes on a printed circuit board (PCB) and then soldered to the opposite side of the board. This type of component is typically larger and more robust than surface mount components, and is often used for high-power or high-voltage applications. Through-hole components are also easier to replace or repair compared to surface mount components.
15.How are 3s pcb battery protection boards designed?
We should perform well in market competition, and the prices of 3s pcb battery protection board products have a great competitive advantage.
Printed Circuit Boards, commonly known as PCBs, are an essential part of modern-day technology. They serve as the foundation for electronic devices and are crucial to their functionality. The process of designing a PCB involves several stages, starting with creating a schematic diagram that outlines the connections between various electronic components. This is followed by placement and routing, where the physical layout of the board is determined and traces are added to connect the components. PCB designers use advanced software to optimize the layout and ensure that it meets the necessary electrical and mechanical requirements. Once the design is finalized, manufacturers can use the design files to produce the PCB. Designing a PCB requires a combination of technical knowledge, creativity, and attention to detail to create a functional and efficient circuit board for a specific application.
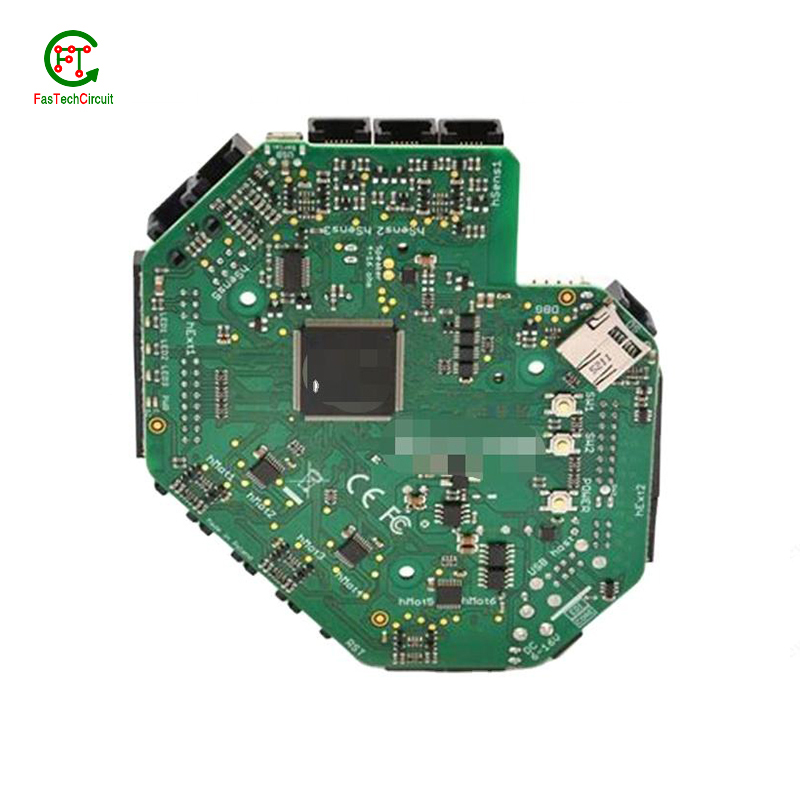
16.What is the purpose of a solder mask on a 3s pcb battery protection board?
We have a good reputation and image in the industry. The quality and price advantage of 3s pcb battery protection board products is an important factor in our hard overseas market.
A solder mask is a thin layer of protective material applied to a printed circuit board (PCB) to prevent solder from bridging between conductive traces, pads, or vias during the soldering process. It also helps to protect the PCB from environmental factors such as moisture, dust, and corrosion. Additionally, the solder mask can provide insulation between conductive traces, reducing the risk of short circuits. It also helps to improve the overall appearance of the PCB by providing a uniform and professional finish.
17.Can 3s pcb battery protection boards be used in high voltage applications?
We have advantages in marketing and channel expansion. Suppliers have established good cooperative relations, continuously improved workflows, improved efficiency and productivity, and provided customers with high -quality products and services.
Yes, PCBs (printed circuit boards) can be used in high voltage applications. However, the design and construction of the PCB must be carefully considered to ensure it can withstand the high voltage without causing damage or malfunction. This may include using specialized materials, increasing the spacing between components, and implementing proper insulation and grounding techniques. It is important to consult with a qualified engineer or designer when using PCBs in high voltage applications to ensure safety and reliability.
18.How are high-speed/high-frequency 3s pcb battery protection board tested and validated?
Testing and validation are essential steps in the production process of high-speed and high-frequency printed circuit boards (PCBs). These specialized types of PCBs are used in a wide range of industries, including telecommunications, aerospace, and automotive, and require precision and reliability in their performance.
The testing and validation process for high-speed/high-frequency PCBs involves several steps to ensure that the final product meets the required specifications. This starts with design simulation and analysis using specialized software to verify the layout and electrical characteristics of the PCB.
Once the design is confirmed, prototype PCBs are manufactured and subjected to various tests, including signal integrity and power integrity tests. These tests evaluate the electrical performance of the PCB, such as its ability to transmit signals at high speeds and maintain signal integrity.
In addition to electrical tests, environmental and mechanical tests are also performed to assess the durability and reliability of the PCB under different conditions, such as temperature changes and mechanical stress.
The final step in the testing and validation process is the inspection and analysis of the tested PCBs. This involves a detailed review of the test results and any necessary modifications to meet the required specifications.
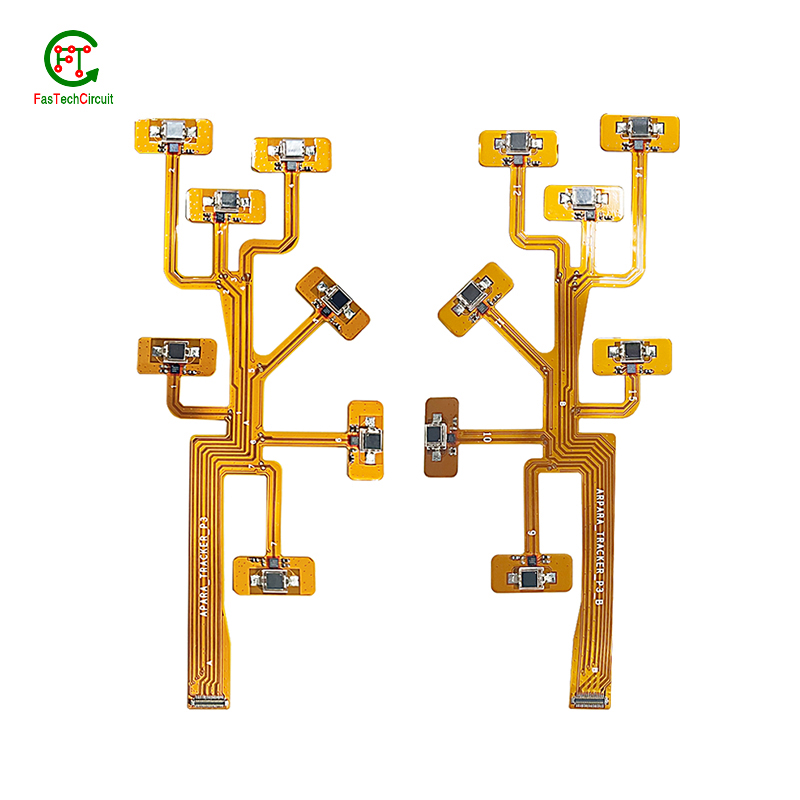
RELATED PRODUCTS & SERVICE
pcb board manufacturing How To Contact US
PCB from 1 to 30 layers, HDI, Heavy Copper, Rigid-flex board with "pcb board manufacturing One-Stop" service.