555 pwm driver pcb layout
FasTechCircuit's products cover single-panel, double-panel, multi-layer boards, rigid boards, flexible boards, hybrid (rigid-soft) boards and other types. According to customer needs and application fields, we can provide PCB products of different materials and processes, such as FR-4, aluminum substrates, ceramic substrates, etc. At the same time, we can also provide a variety of surface treatment processes according to customer needs, such as OSP, HASL, ENIG, etc., to ensure the reliability and stability of the circuit board. We also provide non-standard customization services and can customize production according to the special requirements provided by customers to meet their personalized needs.
FasTechCircuit's printed circuit board products are widely used in communication equipment, industrial control, consumer electronics, computers and peripheral equipment, medical equipment, aerospace and other fields. Our products undergo strict quality control, have high precision, high reliability and stability, and can meet customers' high requirements for electronic products. Our products are very popular in North Korea,Marshall Islands,Tokelau,Ethiopia,Sudan,New Zealand, the United States and Japan. Won high praise from customers.
Number of Layers | 4 layer |
Base Material | gold sinking |
Board Thickness | 2.1MM |
Board Size | 333M*599MM |
Model Number | 4 layer pcb |
Type | pcb |
Place of Origin | Original |
Brand Name | Original |
Copper Thickness | 3OZ |
Min. Hole Size | custom made |
Min. Line Width | custom made |
Min. Line Spacing | custom made |
Surface Finishing | custom made |
Impedance control | +/- 2% |
Warpage | less than 1% |
Packaging Details | New and Original, factory sealed packing, it will be pack in one of these packing type: Tube, Tray, Tape and Reel, Tape and Box, Bulk packing, Bag and etc. Please kindly contact us for more details. |
Supply Ability | 8705 Piece/Pieces per Week |
Quantity (pieces) | > 11667 |
Lead time (days) | 11 |
555 pwm driver pcb layout bearings FAQs Guide Welcome to our state-of-the-art PCB (Printed Circuit Board) products. We are proud to offer a comprehensive range of high-quality and versatile PCB solutions to meet the constantly evolving needs of the modern electronics industry.Our PCBs are expertly designed and manufactured using the latest technology and advanced techniques, ensuring reliability, durability, and exceptional performance for a wide range of applications. We understand the importance of precision and attention to detail in the production of PCBs and we are committed to meeting stringent quality standards.
2.How are high-frequency signals handled on a 555 pwm driver pcb layout?
3.Can a 555 pwm driver pcb layout be used with both through-hole and surface mount components?
4.How are signal traces routed on a 555 pwm driver pcb layout?
5.What techniques are used for reducing electromagnetic interference (EMI) on a 555 pwm driver pcb layout?
6.What is noise coupling and how can it be prevented on a 555 pwm driver pcb layout?
7.What is the power rating for a 555 pwm driver pcb layout?
8.What is the purpose of a ground plane on a 555 pwm driver pcb layout?
9.Can 555 pwm driver pcb layouts be customized?
10.What is the minimum size of a through-hole component that can be used on a 555 pwm driver pcb layout?
11.What are some common 555 pwm driver pcb layout layout guidelines?
12.What is the minimum trace width and spacing on a 555 pwm driver pcb layout?
13.What is the purpose of a solder mask on a 555 pwm driver pcb layout?
14.What software is used for 555 pwm driver pcb layout design?
15.What are some common problems that can occur with 555 pwm driver pcb layout?
16.What are the advantages of using a 555 pwm driver pcb layout?
17.How are 555 pwm driver pcb layouts protected from moisture and humidity?
1.How are components attached to a 555 pwm driver pcb layout?
We adhere to the principle of integrity and transparency, and establish long -term relationships with partners, and we attach great importance to this detail.
eads or pins of the component and melting solder onto them, whicComponents are attached to a PCB (printed circuit board) through a process called soldering. This involves heating the metal lh then solidifies and creates a strong electrical and mechanical connection between the component and the PCB. There are two main methods of soldering components onto a PCB:
1. Through-hole soldering: This method involves inserting the leads or pins of the component through pre-drilled holes on the PCB and soldering them on the opposite side of the board. This method is commonly used for larger components such as resistors, capacitors, and integrated circuits.
2. Surface mount soldering: This method involves soldering the component directly onto the surface of the PCB, without the need for pre-drilled holes. This is done using specialized equipment such as a soldering iron or a reflow oven. Surface mount components are smaller in size and are commonly used for more complex and compact electronic devices.
2.How are high-frequency signals handled on a 555 pwm driver pcb layout?
High-frequency signals are typically handled with great care and precision on a PCB to ensure optimal performance. This involves using high-quality materials, such as high-speed laminates and low-loss dielectrics, to minimize signal loss and interference. Additionally, designers must carefully consider the trace routing and placement of components on the PCB to minimize signal reflections and keep the signal path as short and direct as possible. Specialized techniques, like controlled impedance and shielding, may also be used to further improve signal integrity.
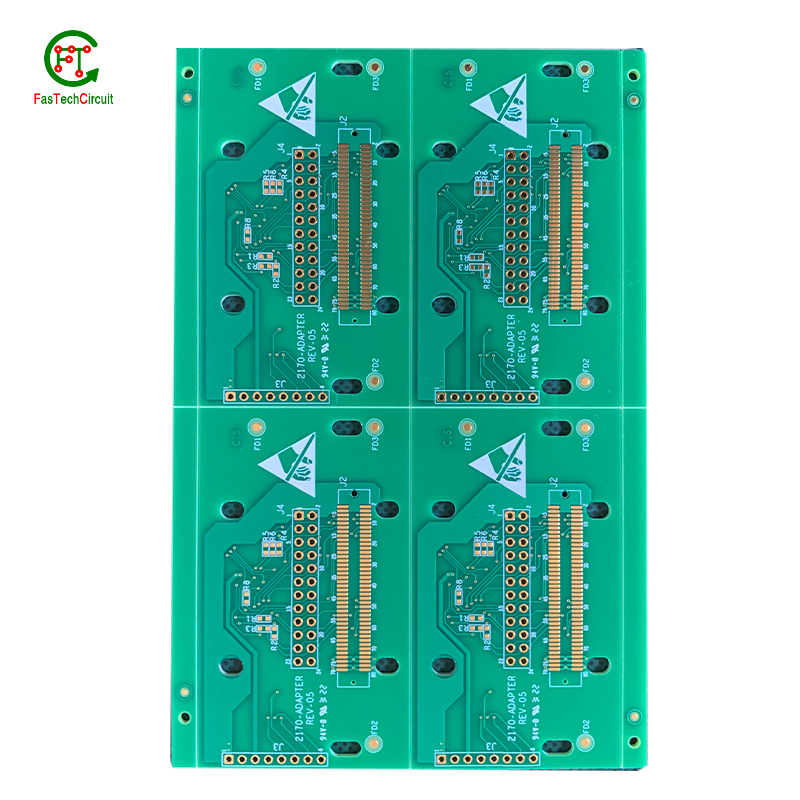
3.Can a 555 pwm driver pcb layout be used with both through-hole and surface mount components?
We continue to improve 555 pwm driver pcb layout products and processes to improve efficiency.
Yes, a PCB (printed circuit board) can be designed to accommodate both through-hole and surface mount components. This is known as a mixed-technology PCB. The PCB will have both through-hole and surface mount pads and traces, allowing for the placement and soldering of both types of components. This type of PCB is commonly used in electronic devices that require a combination of through-hole and surface mount components for functionality.
4.How are signal traces routed on a 555 pwm driver pcb layout?
Signal traces are an essential element of a PCB, responsible for carrying electronic signals between components and ensuring proper communication and functionality of the circuit. To route these traces, designers use specialized software to determine the most efficient and optimal path for each signal, taking into account factors such as signal integrity, trace length, and potential interference. This process involves careful planning, as well as techniques such as vias, ground and power planes, and differential pairs to minimize noise and maintain signal integrity.
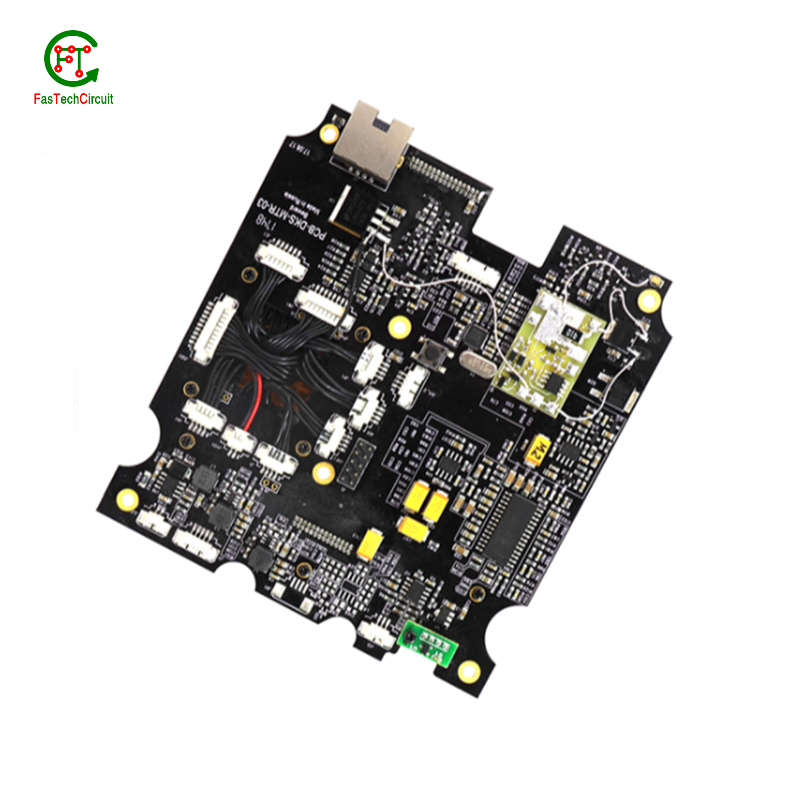
5.What techniques are used for reducing electromagnetic interference (EMI) on a 555 pwm driver pcb layout?
Electromagnetic interference (EMI) is a disturbance caused by electromagnetic radiation that can disrupt the proper functioning of electronic devices. To reduce EMI on a PCB, a number of techniques can be employed. One common technique is to use a ground plane, which acts as a shield to block electromagnetic waves from interfering with the circuit. Another approach is to use proper placement and routing of components and traces to minimize the length of signal paths and reduce the chances of signal crossover. Additionally, using components like capacitors and ferrite beads can help to filter out high-frequency noise. Careful consideration and design of the PCB layout is also crucial in reducing EMI, as the placement, size, and orientation of components can impact electromagnetic emissions. By employing these techniques, EMI on a PCB can be effectively reduced, leading to improved performance and reliability of electronic devices.
6.What is noise coupling and how can it be prevented on a 555 pwm driver pcb layout?
We are a professional 555 pwm driver pcb layout company dedicated to providing high quality products and services.
Signal traces on a PCB (printed circuit board) are routes created to connect electronic components and allow for the transfer of electrical signals. These traces are typically made from copper and are carefully routed and designed to ensure efficient and reliable signal flow. The routing of signal traces is a critical aspect of PCB design and involves determining the best paths for the traces to minimize interference and optimize signal integrity. This is achieved through techniques such as controlled impedance routing, differential pair routing, and length-matching. Properly routing signal traces on a PCB is crucial for ensuring a functional and high-performance electronic circuit.
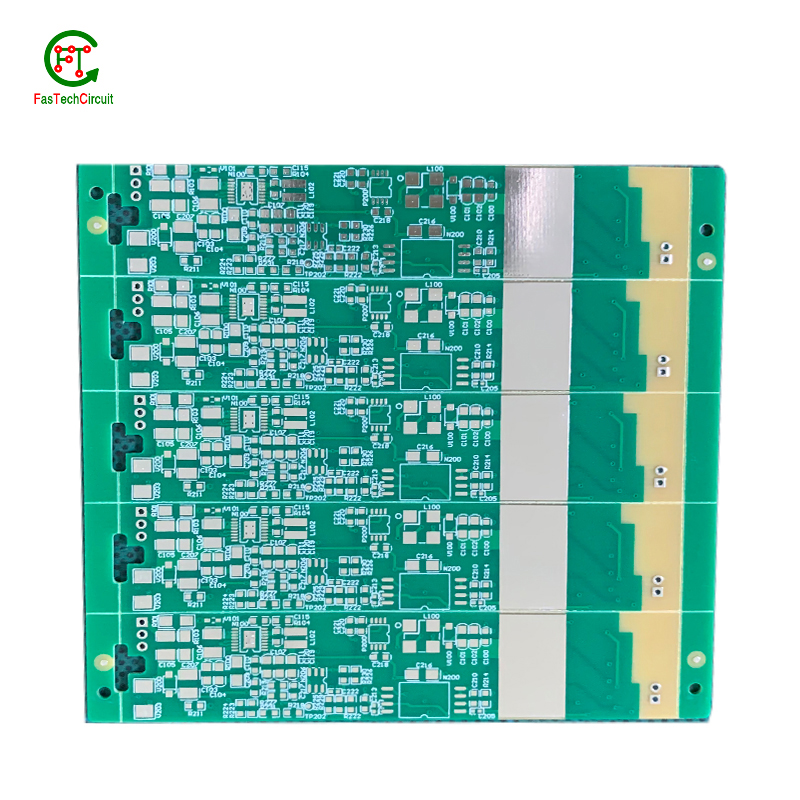
7.What is the power rating for a 555 pwm driver pcb layout?
We maintain a certain amount of R&D investment every year and continuously improve operational efficiency to provide better services to our cooperative customers.
The power rating for a PCB (printed circuit board) can vary greatly depending on its size, design, and intended use. Generally, the power rating for a PCB is determined by the maximum amount of current it can safely handle without overheating or causing damage. This can range from a few milliamps for small, low-power circuits to several amps for larger, high-power circuits. It is important to consult the manufacturer's specifications or consult with an engineer to determine the specific power rating for a particular PCB.
8.What is the purpose of a ground plane on a 555 pwm driver pcb layout?
I have a comprehensive after -sales service system, which can pay attention to market trends in time and adjust our strategy in a timely manner.
A decoupling capacitor is an essential component on a PCB (Printed Circuit Board) which is used to reduce or eliminate high frequency noise between different components. It acts as a buffer between the power supply and other circuit components, by storing electrical charge and then releasing it when there is a sudden change in the supply voltage. This helps to stabilize the power supply, providing a steady and noise-free flow of electricity to the circuit. Furthermore, decoupling capacitors also help to filter out any unwanted signals that may cause interference or disruptions in the proper functioning of the circuit.
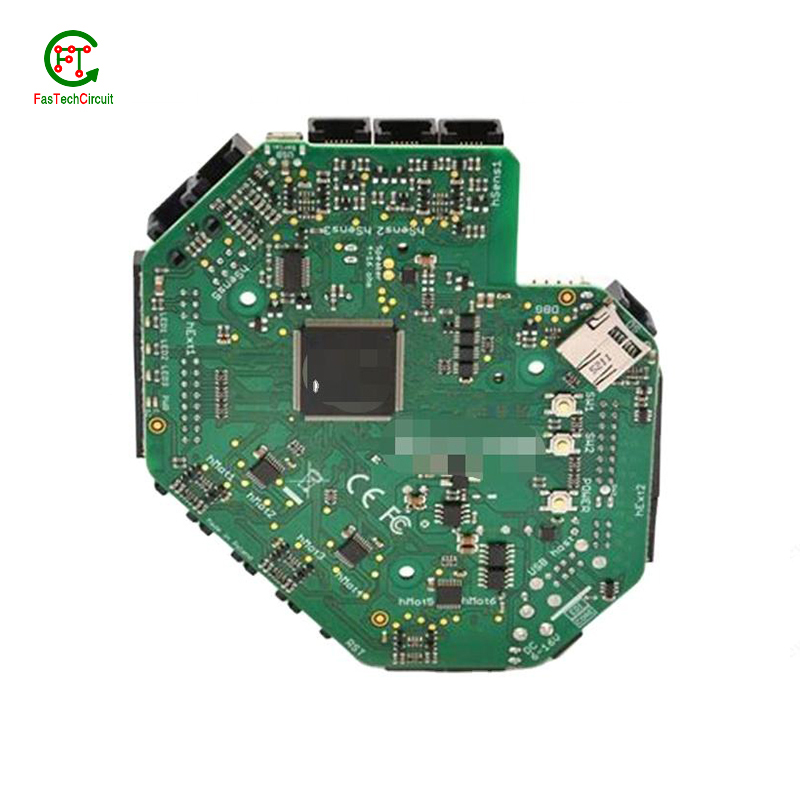
9.Can 555 pwm driver pcb layouts be customized?
We should enjoy a good reputation in the industry, and we can increase the added value of the products of cooperative customers through technological innovation.
Yes, PCBs (printed circuit boards) can be customized to meet specific design requirements. This can include changes to the size, shape, number of layers, and placement of components on the board. Customization can also involve the use of specialized materials, finishes, and manufacturing processes to meet specific performance or environmental requirements. PCB manufacturers often offer design services to help customers create custom PCBs that meet their unique needs.
10.What is the minimum size of a through-hole component that can be used on a 555 pwm driver pcb layout?
We continue to invest in research and development and continue to launch innovative products.
The minimum size of a through-hole component that can be used on a PCB depends on the capabilities of the PCB manufacturer and the design requirements of the circuit. Generally, the minimum size for a through-hole component is around 0.2mm in diameter, but some manufacturers may be able to produce smaller sizes. It is important to consult with the manufacturer and consider the design requirements to determine the appropriate size for a through-hole component on a PCB.
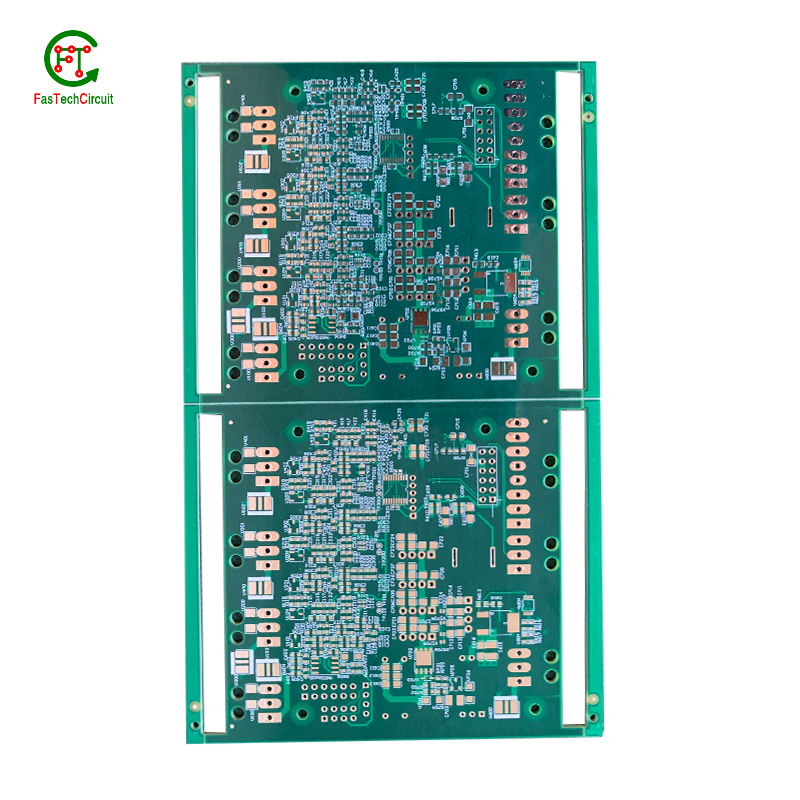
11.What are some common 555 pwm driver pcb layout layout guidelines?
We should have a stable supply chain and logistics capabilities, and provide customers with high -quality, low -priced 555 pwm driver pcb layout products.
Thermal considerations play a crucial role in the design of printed circuit boards (PCBs). The concept of heat management is critical as excessive heat can lead to reduced performance and potential damage to the electronic components on the board. This is why thermal considerations are carefully taken into account during PCB design. Designers must carefully consider factors such as the size, placement, and orientation of components on the board to ensure efficient heat dissipation. They also need to factor in the type and thickness of the board material, as well as incorporate proper ventilation and heat sinks to prevent overheating. By carefully considering these thermal aspects during the design process, the resulting PCBs can perform optimally and have a longer lifespan.
12.What is the minimum trace width and spacing on a 555 pwm driver pcb layout?
We operate our 555 pwm driver pcb layout business with integrity and honesty.
The minimum trace width and spacing on a PCB can vary depending on the manufacturing process and the specific requirements of the design. However, a common industry standard for minimum trace width and spacing is 0.006 inches (0.1524 mm). This is typically used for standard PCBs with a 1 oz copper weight. For more complex designs or higher copper weights, the minimum trace width and spacing may need to be increased to ensure proper functionality and reliability. It is important to consult with the PCB manufacturer and follow their guidelines for minimum trace width and spacing to ensure a successful design.
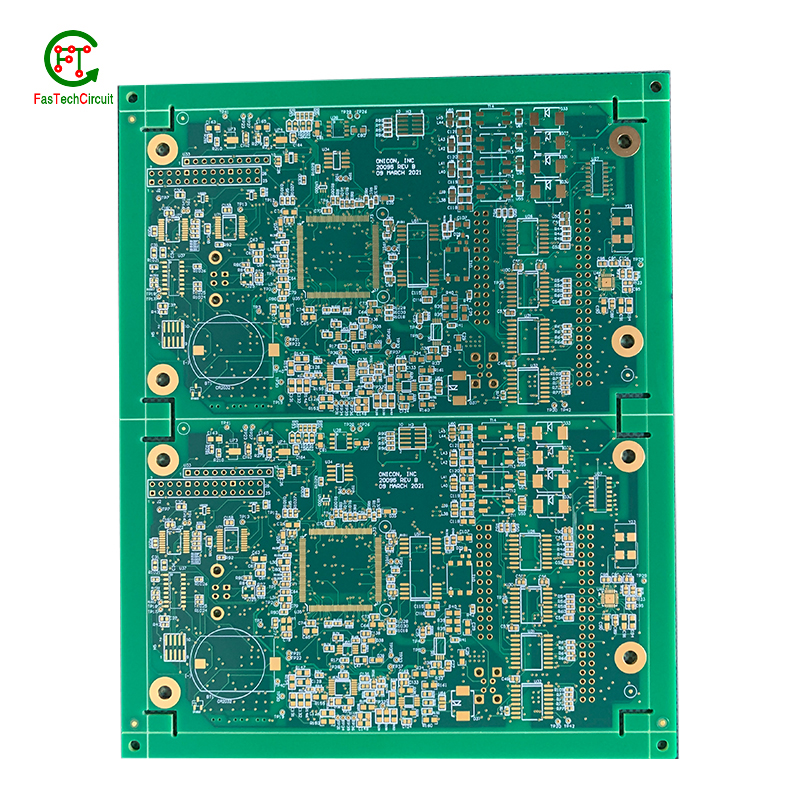
13.What is the purpose of a solder mask on a 555 pwm driver pcb layout?
We have a good reputation and image in the industry. The quality and price advantage of 555 pwm driver pcb layout products is an important factor in our hard overseas market.
A solder mask is a thin layer of protective material applied to a printed circuit board (PCB) to prevent solder from bridging between conductive traces, pads, or vias during the soldering process. It also helps to protect the PCB from environmental factors such as moisture, dust, and corrosion. Additionally, the solder mask can provide insulation between conductive traces, reducing the risk of short circuits. It also helps to improve the overall appearance of the PCB by providing a uniform and professional finish.
14.What software is used for 555 pwm driver pcb layout design?
Our 555 pwm driver pcb layout products have competitive and differentiated advantages, and actively promote digital transformation and innovation.
Some popular software used for PCB design include:
1. Altium Designer
2. Eagle PCB
3. KiCad
4. OrCAD
5. PADS
6. Proteus
7. DipTrace
8. EasyEDA
9. CircuitMaker
10. DesignSpark PCB
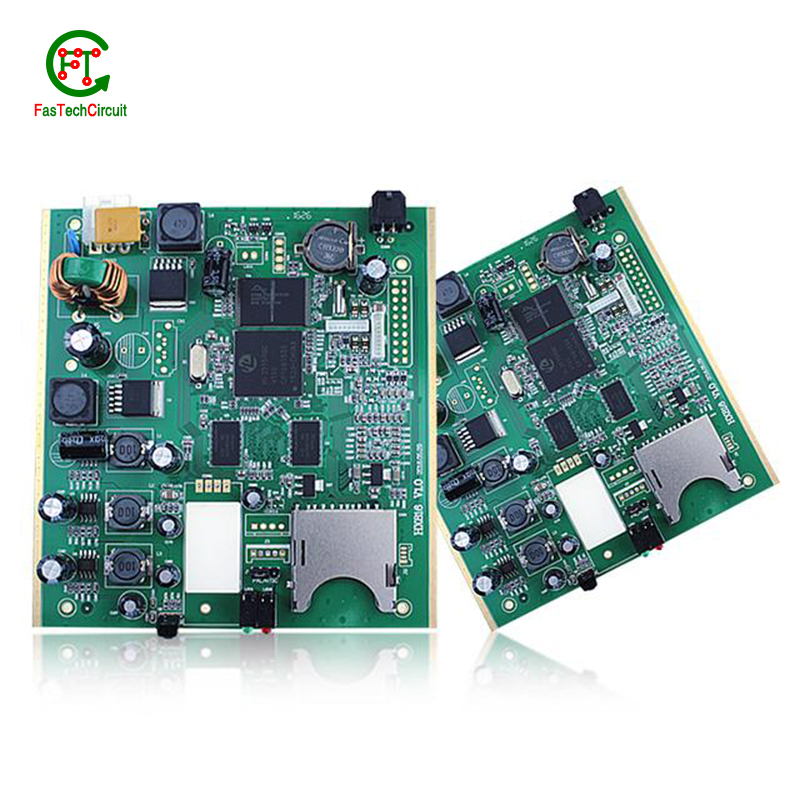
15.What are some common problems that can occur with 555 pwm driver pcb layout?
Our 555 pwm driver pcb layout products undergo strict quality control to ensure customer satisfaction.
PCB (printed circuit boards) are an integral part of electronic devices, serving as the foundation for electrical connections and components. However, like any other technology, there are certain issues that may arise with PCB. One common problem is damage to the board due to excessive heat, as electronic components generate heat and if the PCB is not properly designed or ventilated, it can lead to malfunctions or even permanent damage. Another issue is poor soldering, which can result in weak connections or no connection at all. This can be caused by inadequate equipment or inexperience in the assembly process. Additionally, PCB can also suffer from corrosion over time, especially in high humidity environments, affecting its performance and reliability. It is important to address these problems early on to prevent further damage and ensure the functionality of electronic devices. Regular maintenance, proper design and assembly techniques, and use of quality materials can help prevent these common issues with PCB.
16.What are the advantages of using a 555 pwm driver pcb layout?
We are centered on customers and always pay attention to customers' needs for 555 pwm driver pcb layout products.
There are several advantages of using a PCB (Printed Circuit Board). Firstly, a PCB provides a compact and organized layout for electronic components, which makes it easier for technicians to troubleshoot and repair any issues. Secondly, it reduces the chances of loose connections and short circuits, which can be a major safety concern. Thirdly, PCBs are cost-effective and can be easily mass-produced, making them a popular choice for large-scale production. Additionally, they offer durability and stability, ensuring long-lasting performance. Finally, PCBs also allow for easy integration of new components, making it easier to upgrade or modify the electronic devices.
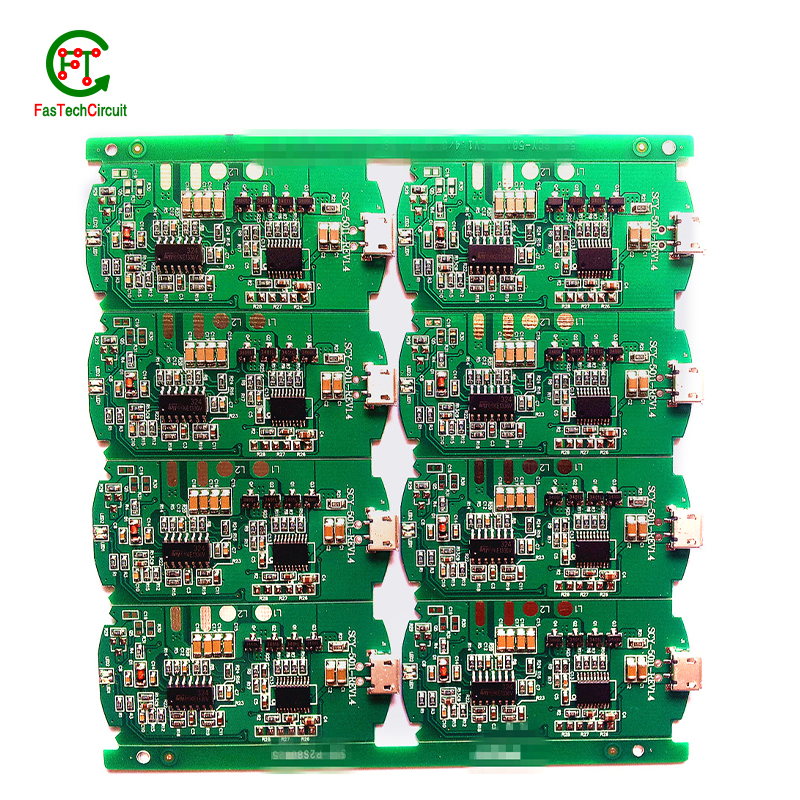
17.How are 555 pwm driver pcb layouts protected from moisture and humidity?
PCB (Printed Circuit Boards) are susceptible to damage from moisture and humidity, which can result in malfunction or even complete failure of electronic devices. Therefore, it is necessary to take measures to protect PCBs from these elements.
One way to protect PCBs from moisture is by using a conformal coating. This is a thin layer of protective material that is applied to the surface of the PCB. It acts as a barrier, preventing moisture from coming into contact with the sensitive components on the board.
Another method is to use moisture-resistant materials for the PCB itself. This can include using moisture-resistant coatings or laminates for the board, as well as corrosion-resistant materials for the conductors and connectors.
In addition to these preventive measures, PCBs can also be stored in controlled environments with low humidity levels. This can help to minimize the amount of moisture that comes into contact with the boards, reducing the risk of damage.
Regular maintenance and periodic testing can also help to ensure the continued protection of PCBs from moisture and humidity. By taking these precautions, electronic devices can maintain their functionality and reliability, even in environments with high humidity levels.
RELATED PRODUCTS & SERVICE
pcb board manufacturing How To Contact US
PCB from 1 to 30 layers, HDI, Heavy Copper, Rigid-flex board with "pcb board manufacturing One-Stop" service.