915 mhz pcb antenna design
Base Material | FR-4/CEM-1/CEM-3/Polyimild/PTFE/Rogers |
Board Thickness | 0.2-7mm |
Model Number | Custom PCB & PCB Assembly |
Type | Aluminum PCB |
Brand Name | FC |
Copper Thickness | 0.4-2mil(7-48um) |
Min. Hole Size | 0.1mm(4mil)for HDI / 0.15mm(6mil) |
Min. Line Width | 0.075mm/0.075mm(3mil/3mil) |
Min. Line Spacing | 0.003'' |
Surface Finishing | HASL/OSP/Ag/ENIG/ENEPIG/Immersion silver/Tin |
Board Size | Custom |
Model Number | Customized |
Base Material | FR4 Aluminum CEM-1 94V0 |
Surface Finishing | HASLENIG OSP |
Number of layer | 1-19layer |
Other service | Components purchasing and assem |
ly Solder mask | White Black Green Blue,Red,etc. |
Dsign service | Available |
Testing | Function testing |
Certificate | RoHS, ISO/TS16949, ISO9001 |
Name | High Quality led light aluminum pcb printed circuit board |
Packaging Details | Vaccum package and standard carton outside High Quality led light aluminum pcb printed circuit board |
Supply Ability | 57382 Square Meter/Square Meters per Month |
Quantity (pieces) | > 14507 |
Lead time (days) | 7 |
915 mhz pcb antenna design bearings FAQs Guide Welcome to our state-of-the-art PCB (Printed Circuit Board) products. We are proud to offer a comprehensive range of high-quality and versatile PCB solutions to meet the constantly evolving needs of the modern electronics industry.Our PCBs are expertly designed and manufactured using the latest technology and advanced techniques, ensuring reliability, durability, and exceptional performance for a wide range of applications. We understand the importance of precision and attention to detail in the production of PCBs and we are committed to meeting stringent quality standards.
2.Can a 915 mhz pcb antenna design be repaired if damaged?
3.How are 915 mhz pcb antenna designs designed?
4.What are the main components of a 915 mhz pcb antenna design?
5.Can 915 mhz pcb antenna designs be used in automotive applications?
6.Can 915 mhz pcb antenna designs be used in high-frequency applications?
7.How are holes drilled into a 915 mhz pcb antenna design?
8.What does 915 mhz pcb antenna design stand for?
9.How are 915 mhz pcb antenna design used in medical devices?
10.Can a 915 mhz pcb antenna design be used for both power and signal transmission?
11.What type of material is used for the silkscreen on a 915 mhz pcb antenna design?
12.How are high-frequency signals handled on a 915 mhz pcb antenna design?
13.What techniques are used for reducing electromagnetic interference (EMI) on a 915 mhz pcb antenna design?
14.How are power and ground planes connected on a 915 mhz pcb antenna design?
15.How are thermal considerations taken into account during 915 mhz pcb antenna design design?
1.How is a 915 mhz pcb antenna design tested for functionality?
A PCB, or Printed Circuit Board, is tested for functionality to ensure that all components and connections on the board are working correctly. This is important in order to detect any potential manufacturing or design defects that could compromise the board's performance. To test a PCB, a range of diagnostic tools and techniques are used including visual inspection, automated testing software, and specialized equipment such as oscilloscopes and multimeters. Experienced technicians also use their knowledge and expertise to troubleshoot and identify any issues with the board. Through this rigorous testing process, any faults or failures are identified and resolved before the PCB is released for production, ensuring that it meets the desired functionality and performance standards.
2.Can a 915 mhz pcb antenna design be repaired if damaged?
We focus on teamwork and communication to achieve common goals, We attach great importance to this detail.
Yes, a PCB (printed circuit board) can be repaired if it is damaged. The extent of the damage and the complexity of the circuit will determine the difficulty and feasibility of the repair. Some common methods for repairing a damaged PCB include:
1. Soldering: If the damage is limited to a few components or traces, they can be replaced or repaired by soldering new components or wires onto the board.
2. Trace repair: If a trace (conductive pathway) on the PCB is damaged or broken, it can be repaired by using a conductive ink or wire to bridge the gap.
3. Component replacement: If a specific component on the PCB is damaged, it can be replaced with a new one. This requires identifying the damaged component and sourcing a replacement.
4. PCB rework: In some cases, the entire PCB may need to be reworked, which involves removing and replacing multiple components and traces.
3.How are 915 mhz pcb antenna designs designed?
We should perform well in market competition, and the prices of 915 mhz pcb antenna design products have a great competitive advantage.
Printed Circuit Boards, commonly known as PCBs, are an essential part of modern-day technology. They serve as the foundation for electronic devices and are crucial to their functionality. The process of designing a PCB involves several stages, starting with creating a schematic diagram that outlines the connections between various electronic components. This is followed by placement and routing, where the physical layout of the board is determined and traces are added to connect the components. PCB designers use advanced software to optimize the layout and ensure that it meets the necessary electrical and mechanical requirements. Once the design is finalized, manufacturers can use the design files to produce the PCB. Designing a PCB requires a combination of technical knowledge, creativity, and attention to detail to create a functional and efficient circuit board for a specific application.
4.What are the main components of a 915 mhz pcb antenna design?
We continuously upgrade our skills and knowledge to adapt to changing 915 mhz pcb antenna design market needs.
A typical PCB consists of several vital components, including a substrate material, copper traces, solder mask, silk screen, and plated through-holes. The substrate material acts as the base and provides mechanical support for the board. Copper traces, usually made of thin lines of copper foil, serve as the conductive paths for transmitting electrical signals. The solder mask, applied as a protective layer, prevents accidental short circuits and corrosion. Silk screen, a layer of ink-based labeling, aids in component identification. Lastly, plated through-holes enable electrical connection between different layers of the PCB board. These components work together to form a fully functioning PCB.
5.Can 915 mhz pcb antenna designs be used in automotive applications?
Yes, PCBs (printed circuit boards) can be used in automotive applications. They are commonly used in various electronic systems in vehicles, such as engine control units, infotainment systems, and safety systems. PCBs offer a compact and reliable way to connect and control electronic components in vehicles. They are also designed to withstand harsh environmental conditions, such as temperature fluctuations, vibrations, and moisture, making them suitable for use in automotive applications.
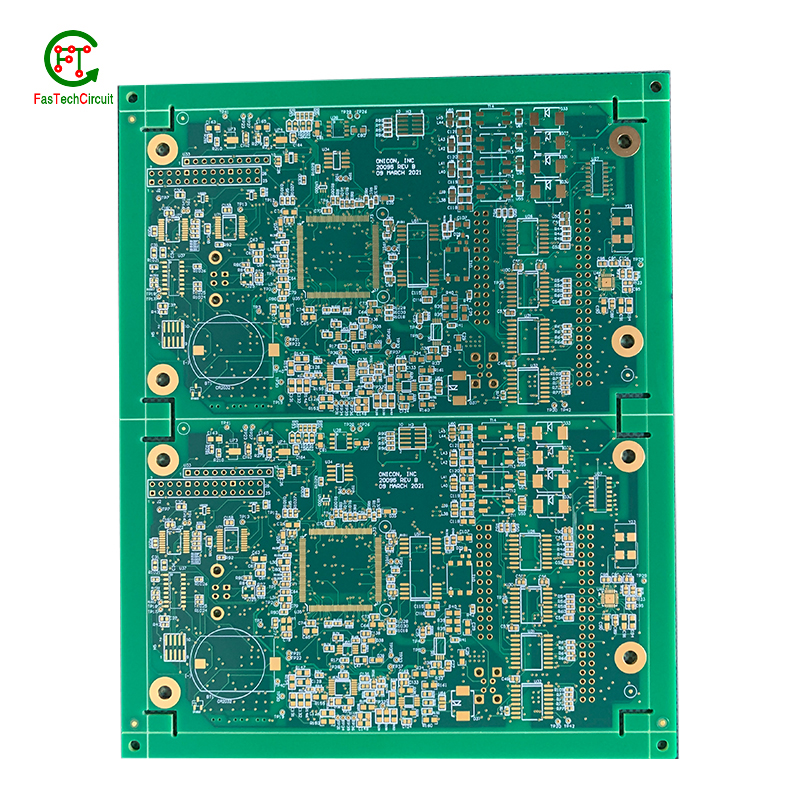
6.Can 915 mhz pcb antenna designs be used in high-frequency applications?
Our mission is to provide customers with the best solutions for 915 mhz pcb antenna design.
Yes, PCBs (printed circuit boards) can be used in high-frequency applications. However, the design and construction of the PCB must be carefully considered to ensure optimal performance at high frequencies. This includes using specialized materials, such as high-frequency laminates, and implementing proper grounding and shielding techniques. Additionally, the layout and routing of the PCB must be optimized to minimize signal loss and interference.
7.How are holes drilled into a 915 mhz pcb antenna design?
We actively participate in the 915 mhz pcb antenna design industry associations and organization activities. The corporate social responsibility performed well, and the focus of brand building and promotion.
Drilling holes into printed circuit boards (PCBs) is a critical part of the PCB manufacturing process. These holes are used for mounting electronic components and for creating electrical connections between different layers of the board. There are two main methods for drilling holes into a PCB – mechanical drilling and laser drilling. Mechanical drilling involves using a high speed drill bit to physically drill through the board, while laser drilling uses a high-powered laser to vaporize the material and create the holes. Both methods have their own advantages and are often used in combination to achieve the desired hole sizes and precision. Regardless of the method, the holes are carefully planned and executed to ensure the successful production of a high-quality PCB.
8.What does 915 mhz pcb antenna design stand for?
We attach importance to the innovation ability and team spirit of employees, have advanced R & D facilities and laboratories, and have a good quality management system.
PCB stands for Printed Circuit Board.
9.How are 915 mhz pcb antenna design used in medical devices?
Printed Circuit Boards (PCBs) are essential components used in a wide range of medical devices, playing a crucial role in both diagnostic and treatment equipment. These devices require reliable and precise circuitry to accurately collect and process data, deliver therapies, and regulate medical procedures. PCBs are used in equipment such as MRI machines, pacemakers, defibrillators, and monitors, where their small size and high density make them ideal for compact and portable designs. In addition, PCBs are also used in medical implants, enabling a safe and secure connection between the device and the body. With their advanced technology, PCBs continue to be an integral part of the medical industry, ensuring the effectiveness and success of various medical procedures and treatments.
10.Can a 915 mhz pcb antenna design be used for both power and signal transmission?
Yes, a PCB (printed circuit board) can be used for both power and signal transmission. This is commonly seen in electronic devices such as computers, smartphones, and other electronic devices. The PCB acts as a platform for connecting various components and circuits, including power sources and signal pathways. The power and signal traces on the PCB are designed to handle different levels of current and voltage to ensure efficient transmission and prevent interference between the two. However, it is important to properly design and layout the PCB to ensure proper separation and isolation of power and signal traces to avoid any potential issues.

11.What type of material is used for the silkscreen on a 915 mhz pcb antenna design?
We have a wide range of 915 mhz pcb antenna design customer groups and establishes long -term cooperative relationships with partners. The countries we provide services include .
The material used for the silkscreen on a PCB is typically a white or black ink made of epoxy or acrylic. It is applied using a screen printing process and is cured at high temperatures to ensure durability and resistance to chemicals and solvents.
12.How are high-frequency signals handled on a 915 mhz pcb antenna design?
High-frequency signals are typically handled with great care and precision on a PCB to ensure optimal performance. This involves using high-quality materials, such as high-speed laminates and low-loss dielectrics, to minimize signal loss and interference. Additionally, designers must carefully consider the trace routing and placement of components on the PCB to minimize signal reflections and keep the signal path as short and direct as possible. Specialized techniques, like controlled impedance and shielding, may also be used to further improve signal integrity.
13.What techniques are used for reducing electromagnetic interference (EMI) on a 915 mhz pcb antenna design?
Electromagnetic interference (EMI) is a disturbance caused by electromagnetic radiation that can disrupt the proper functioning of electronic devices. To reduce EMI on a PCB, a number of techniques can be employed. One common technique is to use a ground plane, which acts as a shield to block electromagnetic waves from interfering with the circuit. Another approach is to use proper placement and routing of components and traces to minimize the length of signal paths and reduce the chances of signal crossover. Additionally, using components like capacitors and ferrite beads can help to filter out high-frequency noise. Careful consideration and design of the PCB layout is also crucial in reducing EMI, as the placement, size, and orientation of components can impact electromagnetic emissions. By employing these techniques, EMI on a PCB can be effectively reduced, leading to improved performance and reliability of electronic devices.
14.How are power and ground planes connected on a 915 mhz pcb antenna design?
Power and ground planes are typically connected on a PCB through vias, which are small holes drilled through the layers of the PCB. These vias are filled with conductive material, such as copper, and allow for the flow of current between the power and ground planes. The vias are strategically placed throughout the PCB to ensure a low impedance connection between the power and ground planes. Additionally, traces or copper pours can also be used to connect the power and ground planes on different layers of the PCB.
15.How are thermal considerations taken into account during 915 mhz pcb antenna design design?
As one of the top 915 mhz pcb antenna design manufacturers in China, we take this very seriously.
Thermal considerations are crucial in the design of printed circuit boards (PCB), as excessive heat can greatly affect the performance and lifespan of electronic components. PCB design engineers must carefully consider thermal management strategies, such as proper placement of heat-generating components, effective heat dissipation techniques, and optimal selection of materials. Thermal simulations and analysis are also commonly used to evaluate and optimize the PCB design to ensure that the temperature of the PCB and its components are within safe limits. By taking into account these thermal considerations, the finished PCB can perform reliably and efficiently, ensuring the overall quality and function of electronic devices.
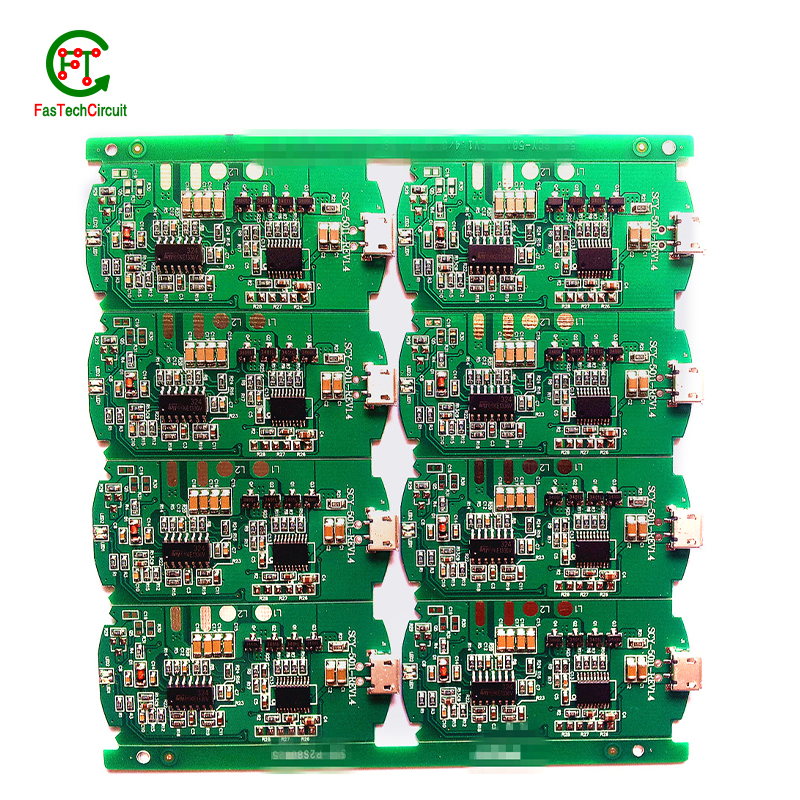
RELATED PRODUCTS & SERVICE
pcb board manufacturing How To Contact US
PCB from 1 to 30 layers, HDI, Heavy Copper, Rigid-flex board with "pcb board manufacturing One-Stop" service.